前言
螺栓连接结构具有紧固、连接、密封等功能,广泛 应用于塔式起重机、施工升降机等设备,是起重机的重 要装配方式。在螺栓服役过程中,常常由于安装不当、 频繁装卸货物、振动、回转、风载等因素影响和外载荷 作用,最终导致螺栓的松弛或断裂,继而引发严重的安 全事故。 近年来,设备运行过程中发生螺栓断裂,严重者造 成起重机倒塌的事故案例屡见不鲜,造成的经济损失与 社会负面影响相当之大。Harish 等[1]的研究表明,紧固 件连接结构主要受轴向载荷、剪切载荷与接触面摩擦力 的作用,这些因素决定了螺栓的塑性变形,影响螺栓的 安全状态。在多个螺栓协同工作以紧固法兰结构的情况 下,整个螺栓组具有一定的容忍度,能够应对少量螺栓 的轻微松动。然而,当失效的螺栓数量逐渐增加时,由 于载荷分布变得不均衡,最终可能导致螺栓发生断裂。 这一从螺栓开始松动到最终断裂的过程,可能会持续数 小时至数天不等[2]。 本文通过超声波的声弹性原理,对受多向载荷的起 重机螺栓进行检测,及时发现应力异常的螺栓,以避免 发生螺栓失效的事故,从而保障起重机械安全运行。
1、超声波检测原理
声弹性效应是使用超声纵波测量螺栓应力的理论基 础,该理论前提是认为固 体是超弹性的,在变形过程中只发生弹性变形。根据声弹性原理基本假设,且当固体各向同性时,可得到 超声波在固体中传播速度和应力之间关系[3,4]。 对于用于紧固连接的螺栓,简化结构如图 1所示。
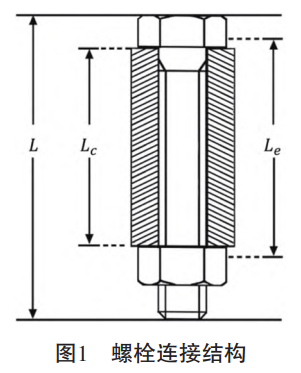
在对螺母施加预紧力时,只有部分螺栓结构受到预紧力 产生的轴向应力,其他部分并没有轴向应力存在。由公 式(1)可知载荷对螺栓 TOF 变化的影响为:

其中:Le为螺栓有效长度,对于铁基合金材料螺 栓,E是弹性模量约为5×1012Pa,CL为超声波应力测量系 数约为-1.5×10-11,同时,σ为应力一般不超过1000MPa。由此可知加载预紧力后超声飞行时间变化量Δt与应 力σ成线性关系,由于螺栓横截面积不变,故超声飞行 时间变化量Δt与预紧载荷F也成线性关系。
2、实验分析
2.1 声弹性数值模拟
建模过程采用毫米(mm)、秒(s)、千克(kg) 单位制,其中螺栓套等材料为Q235D,材料性能参 数:弹性模量为200GPa,泊松比为0.3,密度为7850kg/ m3。连接螺栓采用10.9级的M20高强螺栓,螺栓材料为 30CrMnSi:弹性模量为202GPa,泊松比为0.30,密度为 7850kg/m3。 为了方便固体力学仿真与之后的声弹性效应仿真, 建立单颗螺栓模型,并添加了垫块防止螺栓表面上的横 向载荷过于集中。通常,塔架螺栓在有限元仿真中,由 于螺纹和垫片对螺栓变形影响较小,且螺纹和垫片在网 格划分时会增加计算负担,故在建模时忽略了螺纹和垫 片。为了对对螺栓采用极细化网格,法兰结构采用细化 网格。共有54678个域单元、6747个边界单元和619个边单元。划分后的网格如图2所示。
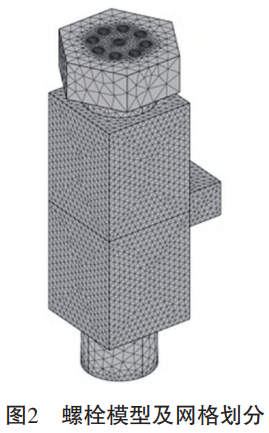
使用COMSOL仿真软件,固定螺栓和法兰的底部, 分别在不同方向对模型施加面载荷,最终对法兰螺栓施 加不同预紧力与横向剪切力后,分别计算不同载荷施 加后模型稳态结果,得到相应的应力分布情况及形变 情况。以20kN为梯度,共三组不同预紧力;以4kN为梯 度,共七组不同剪切载荷。当预紧力固定为40kN时不 同剪切载荷下螺栓的应力分布剖面图如图3所示,当剪 切力固定为40kN时不同预紧力下螺栓的应力分布剖面 图如图4所示。
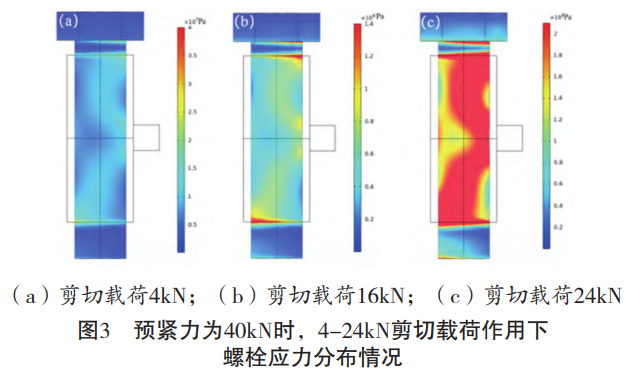
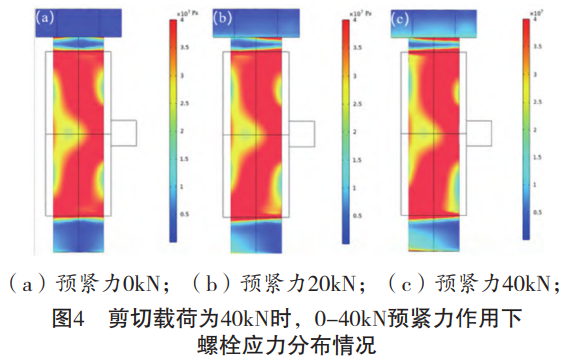
由图3所示,预紧力一定的情况下,剪切载荷施加 在垫块上,垫块与法兰接触的部位显示应力最大,随着 剪切载荷的逐步增加,螺栓内部应力也逐渐增大,由颜 色差异可以区分,螺栓受力的一段由于产生弯曲导致压 缩变形,另一端则出现了拉伸变形。
由图4所示,剪切力一定的情况下,增加螺栓轴向 预紧力,法兰作为横向剪切载荷的载体,其覆盖在螺栓的区域上的应力发生变化,主要是因为螺母施加的预紧 力,减小了螺栓的剪切变形,导致更多轴向方向的应力 发生了变化。最大应力值随着剪切载荷与预紧力的增大 而增大。其中最大应力值为1150MPa,螺栓的屈服强度 为885MPa,预紧力达到40kN时螺栓超过失效强度,故 之后实验只加载至20kN。 使用有限元仿真软件将固体力学与声学仿真模块进 行耦合,从而得到内部存在不同应力分布的螺栓中的超 声波波速与声程的变化,探究不同轴向预紧力与横向剪 切力的作用下超声波飞行时间的变化规律。 图5为螺栓中心截面的声压图,分别是螺栓在40kN 预紧力和24kN横向剪切力作用下,超声传感器中产生 的超声波在3μs、10μs、18.4μs时的传播情况。固定 螺栓端部,对螺栓端面施加轴向的拉伸力,计算出不同 轴向载荷作用下超声波的飞行时间,将飞行时间差与轴 向载荷曲线进行拟合,拟合曲线如图6所示。纵波的线 性拟合方程为y=0.6331x+36800,该拟合曲线的线性回 归系数R2=0.99922。 在施加一定预紧力之后,在垫块处施加横向载荷, 图7是超声传感器在不同预紧力下超声波声时差与横向 载荷变化的关系,可以看到随着预紧力增大,声时-横 向载荷曲线斜率逐渐减小,由2.073减小为1.472。说明 螺母施加的预紧力,减小了螺栓的剪切变形,导致更多 轴向方向的应力发生了变化。
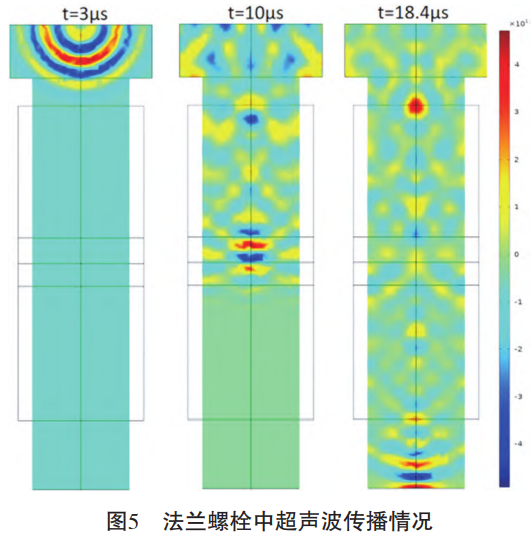
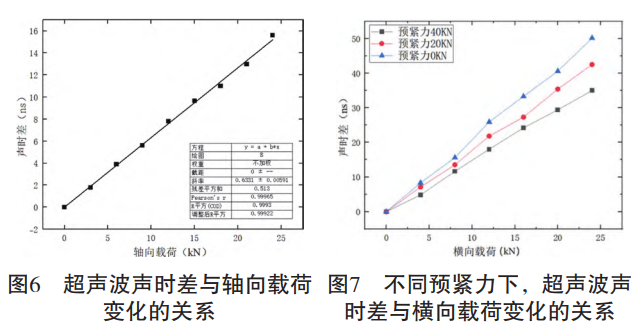
2.2 超声波测量实验
使用合适的夹具和垫片将螺栓固定于拉伸机上,在室温恒定为20℃条件下,通过轴向的拉伸实验,得到了不同轴向载荷作用下中心电极产生超声波的飞行时间,将飞行时间差与轴向载荷曲线进行拟合,拟合曲线如图9所示。其中纵波的线性拟合方程为y=0.93905x+32966,该拟合曲线的线性回归系数 R2=0.99318。可以看到曲线都具有很好的线性度,意味着每当轴向载荷增加1kN,将导致M20法兰螺栓纵波超 声波飞行时间增加0.93ns,将螺栓放入如图8所示的模 具中,通过扳手对法兰螺栓施加不同预紧力后,使用液 压拉伸机对螺栓施加剪切载荷,不同电极的纵横波声时 差随横向载荷变化规律如图10所示。在预紧力一定的情 况下,随着横向载荷的增加,超声波在螺栓中的飞行 时间逐渐变长。预紧力为0kN、10kN、20kN时,螺栓声 时-横向载荷曲线斜率分别为3.74、3.27、2.84,随着预 紧力的增加,声时-横向载荷曲线斜率逐渐减小。 实验拟合曲线与仿真拟合曲线规律基本一致,由于 仿真无法模拟超声设备的真实激发状态,导致实验拟合曲线斜率与仿真拟合曲线斜率有所偏差,但是无论何种 状态,都可以通过标定曲线有效监测螺栓轴力。
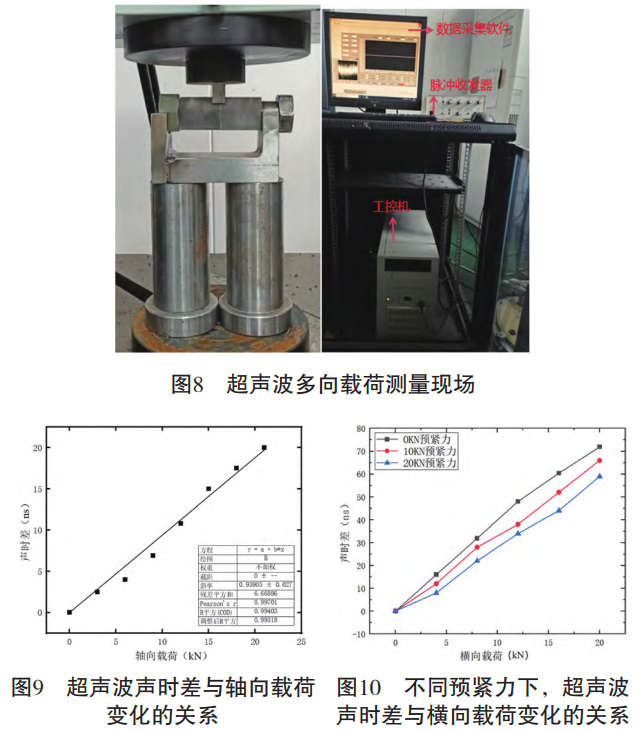
3、结论
1)起重机紧固件在受到单向力时,螺内部应力随 着单向应力的增大逐渐增大,根据实验结果可知,随着应力增加超声波在螺栓中的飞行时间也逐渐增加。
2)当轴向载荷和剪切载荷同时施加时部分应力相 互抵消,随着预紧力的增加,声时-横向载荷曲线斜率 逐渐减小。 基于上述结论,对同批次的起重机紧固螺栓进行多 向载荷的声弹性标定,将超声波飞行时间与所受应力进 行线性拟合,最终获得不同预紧力之下,声时-横向载 荷的标定系数。之后,运用超声探头对服役螺栓进行测 量,对比相应的标定曲线。若声时差所对应的应力与规 定应力不符,则表明该螺栓异常需要及时处理。 总之,上述方法在不损伤待测螺栓的前提下,可以 高效地检测并发现服役起重机中应力异常的螺栓,从而 避免因其失效带来的安全事故。
参考文献
[1] Harish G, Farris T. 铆接接头中微动接触应力对裂纹形成的 影响[C]//39th航空航天结构、结构动力以及材料会议. 1998: 1746.
[2] GL2010. 风机认证指南[S]. 德国:德国劳氏船级社,2010.
[3] 宋文涛,徐春光,潘倩,宋建峰. 残余应力场的超声无损检测与表 征[J]. 中国机械工程学报,2016,29(2): 365-371.
[4] Joseph L. Rose. 固体介质中的超声波[J]. 美国声学学会杂 志,2000,107(4): 1807-1808.
基金项目:湖北省市场监督管理局科技计划项目 Hbscjg-KJ2022004
相关链接