1、 建设背景
近年来, 国家对清洁、 绿色新能源建设, 传统能源的绿色开采及新型设备的投资越来越大。 风力发电作为清洁能源, 属新能源领域重点发展板块,发电机组、 塔筒、 基座及叶根主要采用螺纹副连接, 且多为高强度紧固件。
高强度紧固件生产线建设紧跟国家大力发展风电新能源、 矿山装备、 盾构装备、 桥梁施工等行业 的发展需要, 高强度紧固件每年约有 14 亿件的市场容量, 其中风电新能源、 矿山装备行业的市场需求巨大且持续稳定。 高强度生产线生产的产品要做好针对性服务, 满足行业在技术性能、 个性化需求、 国产化替代等方面对产品的要求。
2、 建设规划与投资规划
建设一条高强度紧固件生产线, 在充分考虑市场规模和企业既有高强度紧固件研发成果转化等各方面因素的情况下, 采取总体规划与分期实施相结 合的思路, 以期采用最小的投资, 覆盖尽量多的产品种类, 形成最大的设计产能和达纲产值。 因此,一期建设的设计方案为保证打通工艺流程, 所有必备工艺设备均须配置到位, 所有信息化必须系统全线贯通, 实现对各工序设备的生产数据采集及 监控。 规划生产线生产的产品种类可涉及风电、 盾构、 矿机、 桥梁等行业的高强度紧固件。 总体规划设计产能可达到 6 700 t/年, 一期建设设计产能1 000 t/年, 后期根据产品市场扩展需求, 分步实 施产线扩能建设。 一期建设预估投资 1 700 万元,配置各类生产设备、 控制及信息化系统、 电缆及设备基础设施等, 并进行安全生产所需的职业健康安全评价、 环境保护评价等。
3 、技术方案
3.1 生产工艺流程
高强度紧固件生产线工艺流程: 原材料倒角→原材料热处理→无心车外圆→校直压光→数控车→冲六方孔→倒角打标→锯切→滚丝→磁粉探伤→包装。
3.2 设备配置及产能规划
高强度紧固件生产线设备配置及产能规划见表 1。
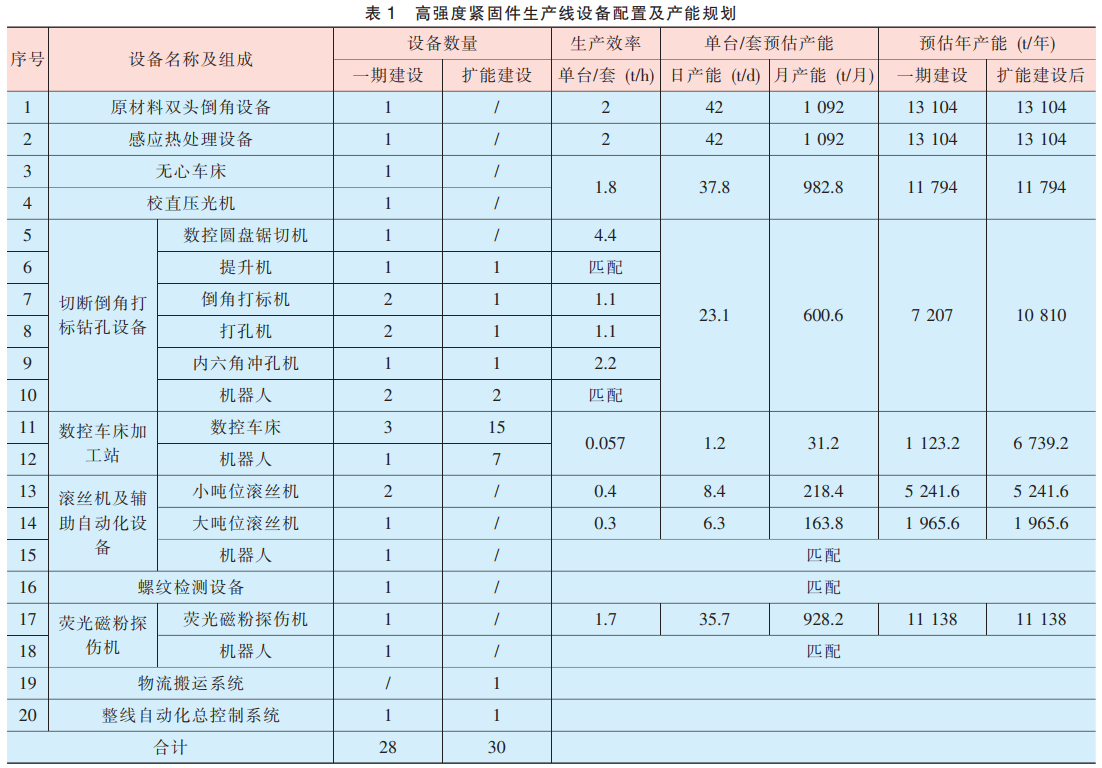
3.3 工艺设备布局方案
项目建设总体规划工艺设备布局方案, 见图1; 项目一期建设工艺设备布局, 见图 2。
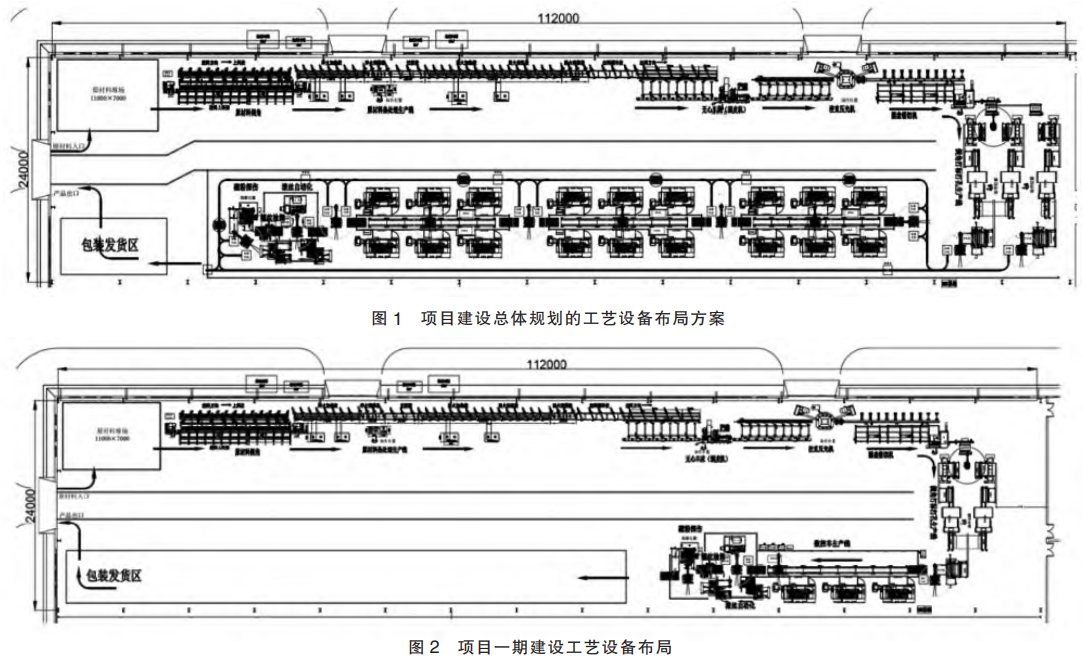
3.4 工艺设备布局方案说明
3.4.1 原材料入场、 倒角及热处理单元布局。
原材料从车间西面大门进入厂房, 在原材料堆场暂存。
近邻原材料堆场, 靠厂房北面依次布置原材料双头倒角设备、 原材料感应淬火回火热处理设备、 无心车床、 校直压光机、 圆盘锯切设备各一套; 设备间均通过辊道、 料架的形式进行生产自动化衔接, 实 现产品在定尺切断及前面各工序连线自动化生产。
3.4.2 锯切、 打标、 打孔设备布局。
在圆盘锯切设备下料端, 由北向南依次布置提升机 1 台、 机器人1 台、 产品双头倒角打标机 2 台、 提升机 2 台、 双工位打孔机 2 台、 六方孔打孔机 1 台、 机器人 1台。 提升机负责接收圆盘锯切机定尺切断后的工件, 并整料后单件提升至固定位置; 机器人负责从固定位置抓取工件并分别放至 2 台双头倒角打标机的料仓内; 双头倒角打标机对工件进行端部倒角打标处理, 再通过输送带将工件输送到后续的提升机料仓内; 提升机将工件整料后, 单件提升至双工位打孔机, 双工位打孔机负责对工件进行端部打底孔。 从两台双工位打孔机出来的产品经过二合一,由输送带送至六方孔打孔机料仓内, 由六方孔打孔机对工件端部打孔加工。 经过打六方孔加工的工件, 在出料口由机器人夹取并有序放置于标准料框内, 待物料转运。
3.4.3 数控加工单元。
后续自东向西布置 18 台数控车床, 用于对工件进行车削加工。 每 6 台数控车床组成一个自动化加工单元, 数控车床两两相对成列布置, 中间由机器人加地轨负责 6 台数控车床的上下料及该加工单元各机床之间的物料搬运。 每个加工单元的进料口和出料口, 由多台物流搬运车实现多个数控加工单元与前后工序之间物料的自动搬运。
3.4.4 滚丝生产单元。
在数控车床加工生产线末端, 近邻布置 3 台滚丝机, 形成滚丝自动化生产单元, 由机器人负责该单元的自动化上料和下料工 作。 完成滚丝的产品, 再由机器人负责转运至螺纹检测设备, 执行滚丝螺纹精度的检测, 并对合格产品和不合格产品进行有序分拣隔离, 后续再由机器人负责将精度合格产品送入荧光磁粉探伤机内, 由该设备对产品进行探伤检验。 经过探伤检验合格的产品进入标准料框内, 转运至包装区进行包装, 不合格的产品进行分拣隔离。
3.4.5 检测检验单元。
当在生产检测过程中出现不合格产品时, 利用隔离工位, 实现物料识别及处置。 生产管控中, 借鉴公司既有的生产经验, 进行可识别的批次化管理, 产品打印永久性标识。 对于同规格、 不同类型产品, 采用合理的生产安排, 进行错时生产, 使产线产品具备生产柔性。
3.5 系统控制
总体规划的设计方案建设完成后, 均采用自动化设备进行生产和物料搬运, 综合考虑车削加工工序的原材料消耗、 工件规格不同等因素, 各工序配置的设备产能基本平衡, 产能匹配合理。 全产线信 息化系统包括数据采集和控制系统 (SCADA)、 制造 执 行 系 统 ( MES) 、 计 算 机 辅 助 工 艺 设 计(CAPP)、 质量管理系统 (QMS)、 能源管理系统(EMS)、 视频监控系统 (NVR), 实现信息化系统对各工序设备的生产数据采集及监控。 关键工序具备在线检测能力, 减少人为因素的干扰, 产品质量稳定性得到保证, 并通过自动化物流设备完成工序 间物流自动化转运, 以此提升转运效率, 减少人员配置, 降低生产成本。 产线满足高标准、 高效率、自动化、 信息化的建设要求。
4 、一期建设技术方案瓶颈及解决
4.1 一期建设技术方案瓶颈
一期建设的设计方案要保证打通工艺流程, 所有必备工艺设备均需配置到位, 所有信息化系统全线贯通, 实现对各工序设备的生产数据采集及监控。 数控车床加工工序配置 3 台数控车床和 1 台机器人形成一套加工单元, 达到一期建设的设计产能满足 1000 t/年, 其余工序设备均具备后期产线扩能的产能, 后期产线扩能建设只需按照市场需求情 况, 增加数控车床、 机器人和物流搬运车等设备,即可快速提升产线产能。 显然, 数控车床加工工序为瓶颈工序。
4.2 数控车床瓶颈工序与前后工序产能暂不匹配的方案
数控车床加工站与倒角打标打孔生产线出料口之间, 设标准料框用于物料缓存。 倒角打标打孔生 产线生产完一批待车削的工件, 然后自动停机, 通 过机器人实现标准料框、 数控车床定位排料架之间的物料搬运, 数控车床加工单元再启动生产程序集 中生产。 待料框清空后, 倒角打标打孔生产线再次启动生产, 重复前述生产流程, 实现连续生产。
数控车床加工站与滚丝自动化生产单元上料口之间设标准料框用于物料缓存。 数控车床工序生产完一批待滚丝的工件, 滚丝机启动加工程序, 通过机器人从缓存料架夹取工件到滚丝机上料机内, 实 现滚丝自动化生产。 待料框清空后, 滚丝机停机待料。 重复前述生产流程, 实现连续生产。
5 、结束语
目前, 高强度紧固件生产线建设项目已完成各项调试工作, 将进入试生产阶段。 借助生产线的实 施, 公司将实现多项新技术、 新成果转化; 同时,也将培养锻炼出一支懂技术、 敢挑战、 勇担当的专 业团队, 为公司未来的发展奠定坚实基础。
作者单位: 黄华,中铁隆昌铁路器材有限公司。
无相关信息