钛合金螺丝在汽车制造领域的应用呈现多维度的技术优势与精细化分工。从型材分类来看,钛螺栓(如轮毂螺栓、发动机紧固螺栓)采用TC4(Ti-6Al-4V)或TA15(Ti-6.5Al-1Mo)材质,通过冷镦或热镦工艺成型,其抗拉强度达900-1200 MPa,比强度为钢制件的2.2倍,M12规格轮毂螺栓单颗重量较钢制件减少40%-50%,全车20颗可降低簧下质量400 g,等效于车身减重4 kg的操控优化效果。钛螺母及垫片则采用TA2(工业纯钛)或TC1(Ti-2Al-1.5Mn),通过精密车削实现六角螺母、自锁螺母等结构,在盐雾测试中耐受5000小时无锈蚀,显著优于不锈钢316L的2000小时标准,同时无磁特性可避免干扰电动车电池管理系统。非标螺丝(如车架专用异形紧固件、传感器支架微型螺丝)采用定制化设计,结合TC4的高比强度与TA15的耐温性(长期550℃/短时800℃),满足发动机舱及涡轮增压器周边的高温高压工况。
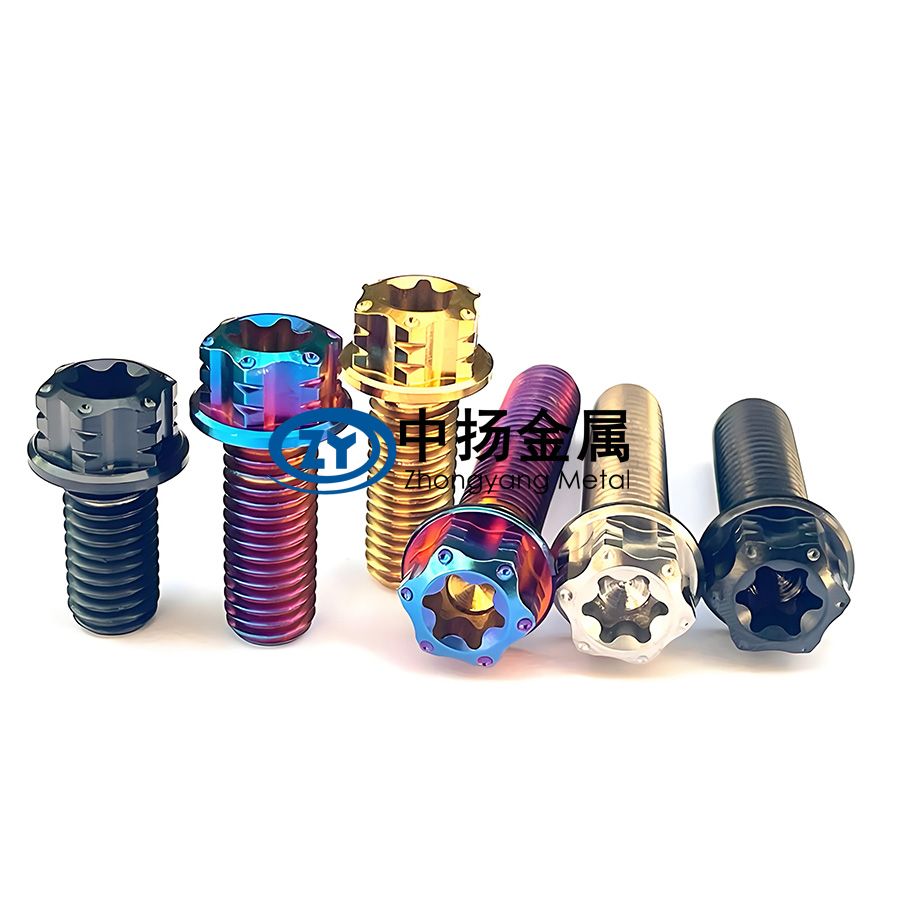
从材质标准体系分析,汽车用钛合金紧固件需符合ISO 5832-3(外科植入物级钛材)、ASTM B348(钛及钛合金棒材)等标准,同时需通过10⁷次振动循环测试以验证预紧力保持率>90%的抗疲劳性能,较钢制件70%-80%的保持率更具可靠性。性能维度上,钛合金螺丝的轻量化边际收益显著,赛车每减重1 kg可提升圈速0.1-0.3秒,而医疗级生物相容性使其能兼容植入式车载医疗设备;耐低温特性(-250℃)则扩展了其在寒区特种车辆的应用场景。当前行业发展趋势显示,钛合金车用紧固件正向高强度(≥1200 MPa级β钛合金研发)、低成本(低合金化TA系列优化)及表面处理创新(阳极氧化炫彩镀层)方向演进,未来在新能源车底盘一体化与氢燃料储存系统领域将形成更深度渗透。
以下是钛合金螺丝在汽车制造领域的深度分析,按不同维度分表呈现:
一、性能优势分析
性能维度 | 钛合金螺丝特性 | 典型应用举例 |
强度-重量比 | 比强度(强度/密度)是钢的2倍以上,减重30%~50% | 特斯拉Cybertruck车架连接螺丝(减重+高承载) |
耐腐蚀性 | 天然抗盐雾、耐酸碱,无需镀层保护(C5级腐蚀环境寿命>10年) | 沿海地区车辆底盘紧固件 |
疲劳寿命 | 高周疲劳极限达500MPa(45钢仅250MPa),抗振动松动 | 发动机悬置螺栓(奔驰AMG系列) |
高温稳定性 | 工作温度上限450℃(TC4合金),优于铝合金(<200℃) | 涡轮增压器周边高温区紧固 |
二、常用材质与牌号对比
钛合金牌号 | 成分特点 | 机械性能 | 汽车应用场景 |
工业纯钛TA2 | 低强度(抗拉350MPa)、高塑性 | 冷成型易加工 | 内饰装饰件轻型螺丝 |
TC4(Ti-6Al-4V) | 综合性能最优(抗拉≥895MPa) | 热处理强化 | 底盘结构件、悬架螺栓(奥迪A8) |
Ti-3Al-2.5V | 高冷成型性、中强度(抗拉620MPa) | 无缝管材衍生产品 | 制动油管接头螺丝(保时捷911) |
β钛合金TB8 | 超高强度(抗拉≥1100MPa)、可焊接 | 固溶时效强化 | 新能源车电池包高强度固定螺丝 |
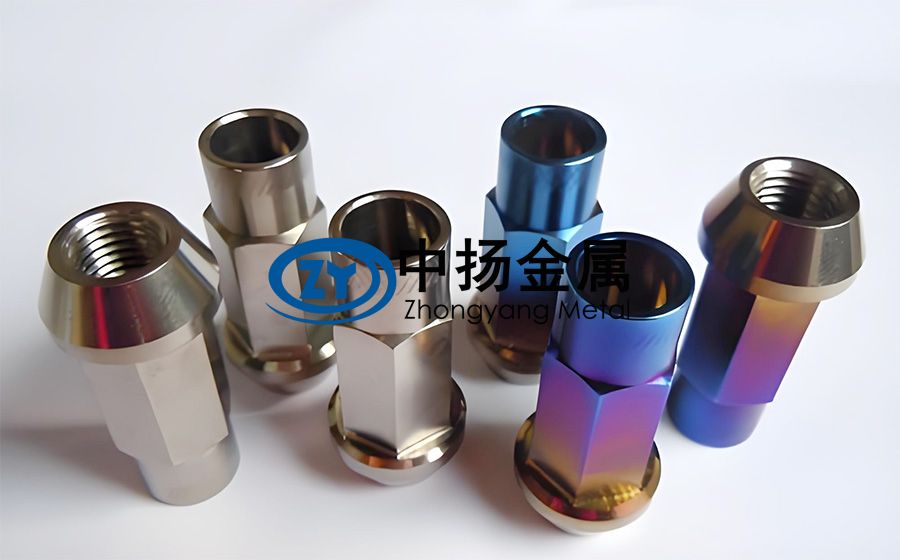
三、制造标准与认证要求
标准类型 | 国际/行业标准 | 核心要求 | 代表企业合规案例 |
材料标准 | ASTM B348(钛合金棒材)、GB/T 2965 | 杂质元素控制(如O≤0.20%、Fe≤0.30%) | 宝马供应商采用AMS 4928航空级标准 |
机械性能标准 | ISO 3506-1(不锈钢与钛螺丝机械等级) | TC4螺丝需满足8.8级(抗拉≥800MPa) | 大众MEB平台电池螺丝符合DIN 912 |
表面处理标准 | AMS 2488(钛合金阳极氧化) | 氧化膜厚度5-25μm,耐电压≥50V | 特斯拉采用MIL-A-8625F军用阳极工艺 |
四、核心制造工艺对比
工艺环节 | 钛合金螺丝工艺要点 | 与传统钢螺丝差异 | 创新工艺案例 |
冷镦成型 | 需预热至200-300℃(降低变形抗力) | 钢螺丝常温成型 | 日本阪村机械开发钛专用温镦机(效率↑30%) |
螺纹加工 | 采用PVD涂层刀具(TiAlN)降低粘刀风险 | 钢螺丝用高速钢刀具即可 | 德国瓦尔特刀具定制钛合金螺纹铣削方案 |
热处理 | 真空固溶处理(防氧化)+时效强化 | 钢螺丝常规淬火回火 | 意大利TAV真空炉连续生产线(能耗↓40%) |
表面处理 | 微弧氧化(MAO)生成陶瓷层(硬度HV≥800) | 钢螺丝镀锌/达克罗 | 比亚迪采用MAO工艺提升电池螺丝绝缘性 |
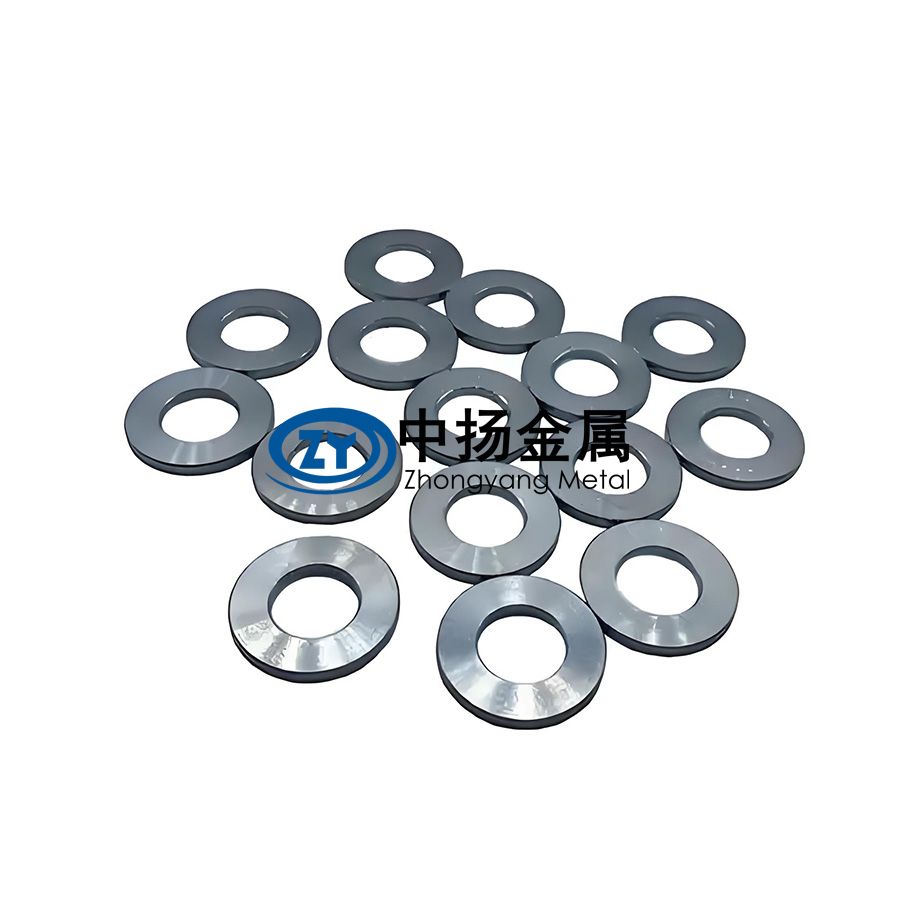
五、与其他材料的综合对比
对比项 | 钛合金螺丝 | 钢螺丝(如8.8级) | 铝合金螺丝(如7075) |
密度(g/cm³) | 4.5 | 7.8 | 2.8 |
比强度(MPa·cm³/g) | 200(TC4) | 102(45钢) | 130(7075) |
成本(元/kg) | 300-600(原材料) | 8-15 | 50-80 |
极限温度(℃) | 450(长期)/600(短期) | 400(需耐热钢) | 150 |
典型失效模式 | 过载断裂(极少腐蚀失效) | 氢脆/应力腐蚀开裂 | 螺纹磨损/蠕变失效 |
六、新兴应用场景探索
应用领域 | 创新应用形式 | 技术优势 | 量产案例 |
新能源汽车 | 电池模组防火紧固(钛+陶瓷涂层防电弧) | 绝缘性+轻量化(电池包减重5kg/车) | 蔚来ET7电池系统采用钛合金防火螺丝 |
智能驾驶 | 激光雷达支架微螺丝(M1.4超小规格) | 高精度(±0.01mm)+抗电磁干扰 | 小鹏G9激光雷达支架螺丝组 |
氢能源汽车 | 储氢罐密封螺栓(抗氢脆特性) | 氢扩散系数仅为钢的1/10 | 丰田Mirai储氢系统专用钛螺丝 |
线控底盘 | 线控转向系统防磁螺丝(非磁性钛合金) | 避免电磁干扰信号传输 | 博世新一代线控转向原型机应用 |
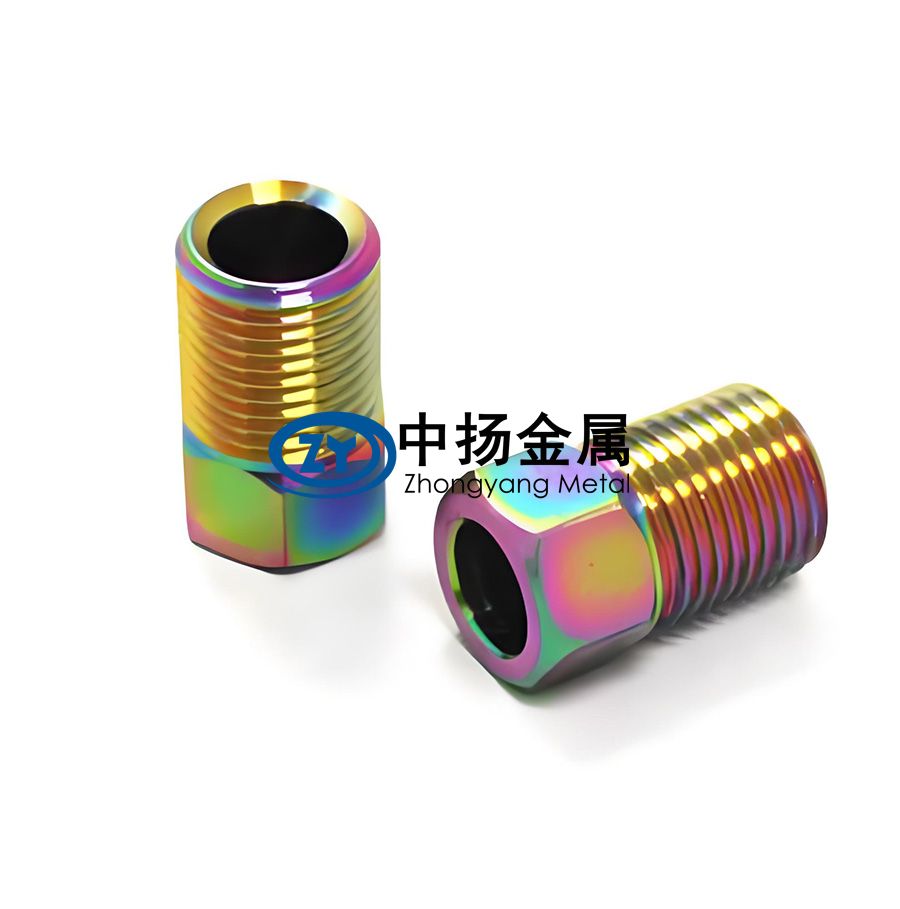
七、市场前景与趋势预测
趋势维度 | 2025年预测 | 2030年展望 | 驱动因素 |
市场规模 | 全球汽车用钛螺丝达12亿美元(CAGR 18%) | 超30亿美元(新能源车渗透率>40%) | 轻量化政策(如欧盟CAFE标准) |
技术突破 | 冷锻钛合金普及(成本降30%) | 3D打印拓扑优化钛螺丝(减重50%) | 增材制造技术成熟度提升 |
区域发展 | 中国占比35%(宁德时代/比亚迪供应链需求) | 东南亚新兴市场崛起(泰国/印尼电动车产能) | RCEP区域零关税政策 |
材料替代率 | 高端车型钛螺丝占比8% | 全行业平均替代率15%(豪华车达30%) | 碳关税倒逼材料升级 |
八、选型决策指南
选型因素 | 优先选钛合金的条件 | 推荐牌号 | 替代方案 |
轻量化需求 | 减重效益>成本增量(如每减1kg成本允许增加¥200) | TC4(通用)、TB8(超高强) | 碳纤维复合螺丝(更高成本) |
腐蚀环境 | 盐雾测试>1000h或酸性介质环境 | TA2(普适)、TC4(强化) | 不锈钢+涂层(寿命较短) |
高温场景 | 长期工作温度>300℃(如排气系统) | TC4、Ti-6242(耐650℃) | 镍基合金(成本高2-3倍) |
电磁敏感区 | 要求非磁性(如传感器周边) | β钛合金(TB8、Ti-15Mo) | 铜合金(强度不足) |
结论
性能驱动:钛合金螺丝凭借 超强比强度+耐腐蚀 成为高端汽车首选,但需通过工艺创新降本;
技术迭代:温镦成型+微弧氧化等工艺突破正缩小与钢螺丝的价差;
应用爆发点:新能源三电系统(电池/电机/电控)将贡献70%以上增量需求;
选型策略:建议在 安全关键件+高附加值车型 优先导入,逐步向主流车型渗透。
相关链接