1、引言
钛合金具有比强度高、重量轻、耐腐蚀、导热率小、弹性模量小、非磁性及线膨胀系数小等特性,是再生冷却结构推力室喷管的理想材料[1]。相同量级发动机若采用钛合金喷管可以减轻重量,大幅提高发动机的推质比,使液体火箭发动机的综合水平得以提升,有效提高运载火箭发动机的运载能力[2]。
现役液体火箭发动机推力室扩张段内外壁多采用不锈钢材料,不锈钢虽具有良好的塑性和切削性能,但相较于低密度且高强度的钛合金,在液体火箭发动机扩张段上的应用劣势较为明显,推质比大打折扣,对发动机性能提升有较大的制约。

随着我国制造生产水平和工艺技术的稳步提升,已经在某大型液体火箭发动机推力室扩张段上应用了钛合金材料。虽然钛合金材料具有独特的优势,但其加工工艺难度大,不仅在钣金热成型工艺中较不锈钢的成型精度差,而且切削加工性较低,主要体现在:钛合金导热性能差,切削过程产生的切削热聚集在工件与刀具的接触区域,刀具磨损快,非特制切削液不能发挥良好的冷却效果;钛合金在温度600℃以上时硬度显著上升,加速刀具磨损;钛合金塑性低,弹性变形大,加工过程中已加工表面与刀具后刀面的接触面积增大,降低切削性能[3]。
液体火箭发动机推力室扩张段内外壁均属钛合金大型薄壁结构件,针对其难加工特性,通过专用刀具开发、程序优化和参数优化等技术手段,经大量的切削试验验证研制出适用于钛合金大型薄壁件的工艺技术方案,使加工效率获得显著提升。
2、零件加工技术难点
2.1零件结构特点
某型液体火箭发动机推力室扩张段内壁(简称内壁)小端直径约1000mm,大端直径约1800mm,大小端端面距离约1300mm,壁厚4mm,径厚比250~450,且内壁铣槽后槽底剩余壁厚最小为0.6mm,径厚比高达3000,属于典型的大型薄壁件。内壁由钛合金钣金件拼焊胀型而成,胀型过程中,内壁壁厚经历剪切—拉伸复合运动,是多因素综合作用下的弹塑性变形过程,由于母线为非线性曲线,内壁不同部位的壁厚变化量不同。
钛合金材料弹性模量小、常温下塑性差、各向异性系数大、成型后回弹大且冷成型极易开裂,导致内壁的钣金成型难度极大,需采用热成型模式,而热成型对零件的形状、表面质量和尺寸精度影响很大,在大尺寸薄壁曲母线钛合金内壁中表现更为明显。在整个热成型过程中,成型温度区间、间隙选择、进给率和主轴转速等因素对产品精度控制有很大影响,造成其表面轮廓度差,与设计理论型面偏差较大,所设计的工装无法与其平稳紧密贴合,尤其在大端轴向400mm范围内存在大面积未贴合现象。
工件需加工近300条纵向均布直槽,倘若刀具寿命不稳定,频繁换刀将占用大量生产时间。
在加工过程中,拼焊、胀型时形成的应力会缓慢释放,工件局部产生变形,容易造成产品几何尺寸超差;另一方面,工件表面均布近300条槽,壁厚由4mm减薄到0.6mm,金属去除量大,这一过程会同时出现应力的产生与释放,同样会促使产品变形,造成工件与工装局部不贴合。图1为产品结构示意图。
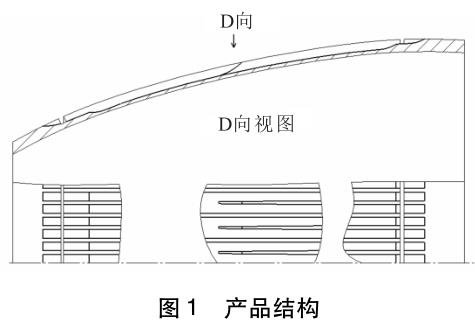
2.2加工技术难点
钛合金材料固有的特性决定了其切削性能差,钛合金大型薄壁件不仅具备钛合金材料难切削的特点,而且铣槽毛坯钣金件的刚性差,更加剧了铣槽加工难度。与其他碳钢相比,钛合金与刀具材料件的摩擦系数更大,而切屑变形系数远小于其他材料,切屑与前刀面的摩擦速度大,接触界面温度高,刀具更易磨损[4]。钛合金在高温下化学活性高,能与空气中的氢、氧、氮发生化学作用形成脆性层,降低材料塑性,并使切屑与前刀面的接触长度减小,加剧刀具磨损。
由于钛合金大型薄壁件成型难度大且型面精度差,内壁与工装胎具不贴合,刀具切削加工过程中抗振性差,刀具磨损严重,难以保证槽深和筋宽等技术指标,产品报废率高。
该型号内壁结构尺寸远大于现有铣槽件,由于现有铣槽设备的装夹空间、承重能力和采样软件处理能力不足,对于大型薄壁件的装夹存在困难。
钛合金铣槽时存在刀具磨损严重和报废频繁等问题,加工一件产品因崩刃、断齿等原因会报废高速钢铣刀约100片,高速钢刀具加工钛合金的适用性低。虽然硬质合金刀具比高速钢刀具更适合铣削钛合金,但由于冷却不足,单件内壁需消耗硬质合金铣刀约30多片,耗费刀具价值约10万元。为充分冷却需使用大流量乳化液浇注(流量>5L/min),造成冷却液大量耗费且污染环境。
由于频繁换刀及返修刀具损坏造成尺寸超差,铣槽效率低,加工1件钛合金产品用时约480h,而同样结构尺寸的不锈钢产品仅需160h。
以上技术难点导致钛合金薄壁件喷管铣槽加工存在质量差、物耗能耗高、清洁程度低、加工效率低以及生产周期长等问题,改进钛合金薄壁件铣槽工艺技术改革方案势在必行。
3、解决方案
为解决钛合金薄壁件内壁的铣槽加工难点,本文通过专用刀具、切削参数和加工方法三个方面对其进行工艺研究。
3.1刀具方案
分别采用现有的超硬高速钢锯片铣刀、涂层高速钢锯片铣刀和涂层硬质合金锯片铣刀进行加工实验,每种锯片铣刀采用相同的切削参数,对钛合金试板进行铣削加工,实际切削长度如表1所示。
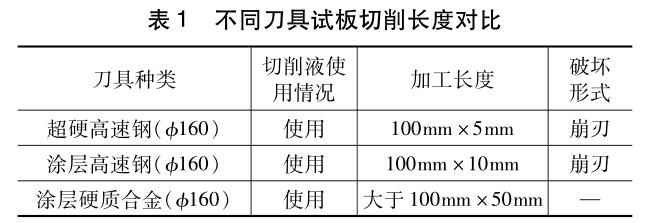
通过钛合金试板铣削实验对比,在试板贴和良好的情况下,涂层硬质合金片铣刀的耐用性和耐磨性均远好于高速钢片铣刀。
通过对试板的加工,初步掌握了钛合金片铣刀的切削转速、切削深度及进给量的选用范围。
考虑到实际产品的加工长度和贴合情况远比试板的装夹情况差,且大端存在轴向400mm范围内与胎具不贴合的情况,使用三组刀具在最佳转速和切削深度的情况下对产品进行试加工,加工情况如表2所示。
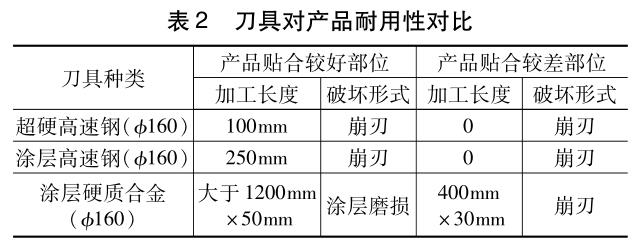
通过实验对比得知,在产品贴合较差的部位,由于切削过程中产生的振动很大,容易对刀具造成结构性破坏,导致刀具的使用寿命大幅下降。
涂层硬质合金片铣刀的失效形式也由涂层磨损变成了崩刃,如图2所示。
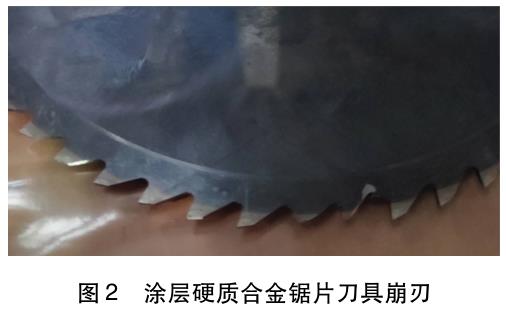
具崩刃不仅极易造成产品扎刀,而且大幅降低了整体式硬质合金片铣刀的耐用性。在降低产品质量的同时,提高了加工成本,因此需要针对产品特点对加工参数和加工方法进行优化。
3.2加工方法与参数优化
3.2.1加工技术
火箭发动机扩张段内壁再生冷却通道铣削加工技术依托数字化激光仿形直槽铣槽机加工[5],具有如下特点:①以铣槽处外表面作为母线基准,采用激光微位移传感器对每条槽对应的外表面进行扫描采样,消除了采样位置与铣槽位置不一致带来的槽深误差;②对于要求剩余等壁厚的铣槽件,不仅外表面母线采用精确的激光采样技术,而且以工件的实际原始壁厚为依据建立工件壁厚数据库,通过软件获取槽底轨迹,精确控制槽底剩余壁厚;③该技术不仅能加工等槽深和等剩余壁厚的槽,而且能在同一条槽上完成指定槽深加工,将原来多道工序合并为一道工序,提高加工质量的同时提升了加工效率。
喷管数字化加工工艺流程见图3。
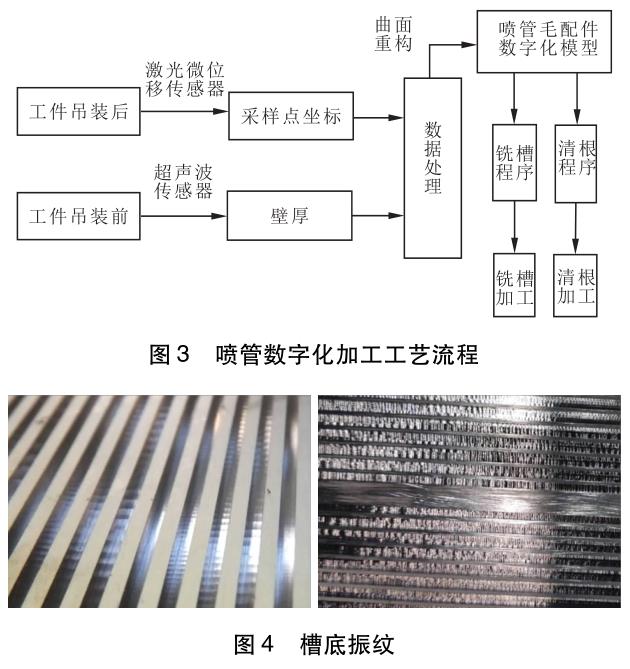
3.2.2加工方法
试加工时,在贴胎较差部位出现刀具寿命大幅降低的情况,同时刀具磨损导致铣槽槽底因振动产生振纹(见图4)。由于产品不贴胎,导致钛合金薄壁固定性差,钛合金材料的切削回弹现象被成倍放大,在按相同切削深度的数控程序加工情况下,产品贴胎较差部位比贴合良好部位最终槽深要浅0.3~0.5mm,严重超出设计范围。
解决上述问题,针对激光采样仿形得到的型面结合产品的实际贴合状态,采用分区域处理。通过调整进给速度和槽深回弹补偿分区域对各种贴合状态进行独立设计加工参数,保证铣槽光洁度和槽深尺寸满足设计要求。
钛合金的弹性模量仅有钢的一半且屈强比大,在切削加工时钛合金零件容易产生较大变形。扩张段II段内壁大端超过250mm范围内不贴胎,铣槽时出现让刀现象,每条槽的槽深不一致(见表3),大端不贴胎处的槽深较贴胎处浅0.2~0.3mm,主辅两个铣头加工区域的槽深误差和贴胎情况不一致。针对上述情况,采取下列措施来解决槽深超差问题。

(1)主辅侧分别单头加工。
(2)轴向分段铣槽,分别控制槽深。
检测每条槽的槽深,标注槽深超差区域。
经过分析、辨别、比对,不贴胎区域的槽深与贴胎区域槽深差别较大,将是否贴胎作为分段加工的界限。每条槽在整个槽长范围内整体采样,在进行加工程序处理时设置不同的槽长,轴向分两段加工。距大端250mm作为分段界限,先加工贴胎情况较好区域,距大端250mm开始至小端铣槽结束,此区域贴胎较好,采用原来的加工参数,连续加工数十条,具体条数根据周向圆跳动决定。大端开始至距大端250mm处作为第二段铣槽区域,为了保证两端能够很好地对接,铣槽位置超出250mm。
(3)两端分别采用不同的加工参数。
靠小端区域贴胎情况好,无让刀现象,大端区域不贴胎且刚性差,铣槽时存在让刀现象,在铣槽深度设置时注意监控槽深。
主轴转速为96r/min,进给量为44~66mm/min。
(4)采用高速钢铣刀加工贴胎好的区域,剩下的不贴胎区域留给硬质合金铣刀加工。虽然采用分段加工,但是大端不贴胎区域依然断刀频繁,铣槽较难。为了加快研制进度,采用高速钢铣刀暂时加工贴胎良好的区域,贴胎不好的大端采用硬质合金铣刀铣槽。
钛合金薄壁件与胎具的贴合间隙为0.1~3mm,通过分区域加工技术,不仅保证了在该贴合状态下的最快加工速度、加工效率和刀具耐用度,大幅降低了加工成本,而且可以通过对该区域的铣槽深度进行参数补偿,保证产品整体槽深的一致性。
3.2.3参数优化
钛合金对变形速度敏感,应在低速条件下进行加工。钛合金弹性模量低、回弹大、易变形以及弹性模量低,已加工表面容易产生较大回弹,而且薄壁零件的回弹更为严重,会引起零件在机加工过程中刀具偏离,难以保证产品精度。
需要进行钛合金铣槽加工参数的研究(主轴转速、吃刀深度和切削速度等),解决钛合金回弹带来的加工精度下降。
经试验验证,硬质合金铣刀最佳切削参数为进给量0.015mm/z,刀具直径φ154mm~φ160mm,齿数Z=32,主轴转速S=180r/min,进给速度选择F=90mm/min。每齿进给量=F/(S×Z)=90/(180×32)=0.0156mm。
不贴胎处选择主轴转速S=90r/min,进给速度选择F=44~66mm/min最佳。
优化前后的加工工件对比如图5所示。
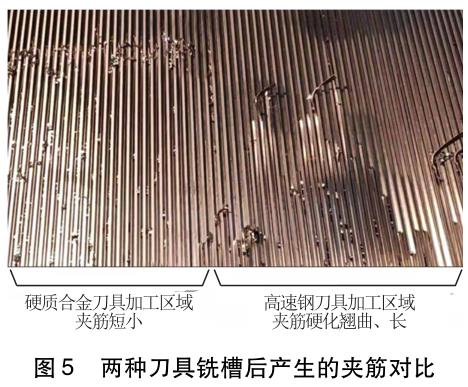
结语
本文解决了某型液体火箭发动机推力室扩张段内壁的钛合金铣槽难题。该技术不仅大幅缩短了加工周期,节省了加工成本,极大提升了液体火箭发动机的整体性能,具有良好的经济效益和社会效益。
通过对专用刀具开发、切削参数优化和加工方法提升三个方面的研究,得出以下结论。
(1)钛合金材料大型薄壁件铣槽刀具优先采用硬质合金材料的锯片铣刀,无论是刀具耐用度、加工效率、铣槽质量还是加工用的高速钢锯片刀具都比硬质合金锯片刀具更差。
(2)大型薄壁件刚性差,铣槽夹具的设计很关键,适当的胎具装夹可以解决整体加工系统刚性差的问题。
(3)钛合金材料大型薄壁件的贴胎程度对铣槽槽深有明显影响,可以采用分片加工的工艺方法解决不贴胎造成的让刀问题。
(4)钛合金材料大型薄壁件的贴胎程度对刀具耐用度以及产品表面质量有较大影响,后续要着力解决钛合金材料大型薄壁件的成型问题,确保与胎具贴合。
(5)采用数字化仿形铣槽技术可以解决大型薄壁件轮廓度差的问题。
参考文献
[1]吕嗣孝,周洪,崔建坤.钛合金材料切削加工参数优化和实验研究[J].机械工程师,2022(1):154-156.
[2]谭永华.中国重型运载火箭动力系统研究[J].火箭推进,2011,37(1):1-6.
[3]朱卫华,王宗园,任军学,等.TC4钛合金薄壁件铣削残余应力变形研究[J].组合机床与自动化加工技术,2020(12):70-72,79.
[4]闫凯强,黄晓斌,张仕杰,等.面铣刀铣削钛合金时切削参数对切削力影响规律的仿真[J].工具技术,2022,56(4):80-83.
[5]卢杰持,胡力耘,杨金奎,等.火箭大喷管数控仿形铣槽控制系统[J].大连理工大学学报,1998,38(3):296-299.
第一作者/通信作者:刘林,硕士,高级工程师,西安航天发动机有限公司,710100西安市
FirstAuthor/CorrespondingAuthor:LiuLin,Master,SeniorEngineer,Xi′anSpaceEngineCompanyLimited,Xi′an710100,China
无相关信息