钛及钛合金板、带、箔材在钛加工材的生产和应用上均占有重要地位。根据中国有色金属工业协会的统计数据,2021年度中国钛加工材的总产量为 135941 t,其中钛及钛合金板、带、箔材的产量为 70130 t,占钛加工材总产量的 51.6%。钛板材是指通过平面轧制 获得厚度≥0.3 mm 的片状产品,钛带材是指通过平面轧制获得厚度为 0.1~ 4.76 mm 的卷状产品,钛箔材是指通过冷轧和退火多次循环得到厚度 < 0.25 mm 的片状产品,以上3种产品可以统称为钛平面轧制产品。钛板、带、箔材主要应用于化工、航空航天航海和医疗3大板块。其中,纯钛带材主要用于化工行业,纯钛板材用于航空航天航海和医疗领域,合金板材、箔材主要用于航空航天航海领域。

根据化学成分、产品规格和使用需求的不同,钛及钛合金板材的制备技术有较大区别。在轧制成形工艺上,钛板材根据厚度不同可以分为厚板(厚度 >4.76 mm)和薄板(厚度 ≤4.76 mm),通常厚板通过热轧到成品尺寸,薄板则可以选择性地通过单片热轧随后冷轧到成品尺寸,或 者包套叠轧到成品尺寸。厚板的轧制过程可以通过控制轧制温度、轧制方向和变形量调控组织与性能。合金薄板的制备过程采用两片叠轧和包套轧制 工艺可以提高变形量和轧制效率。此外,采用包套轧制工艺可以制备变形抗力较大和裂纹敏感性较高的合金薄板。在轧制装备上,国内外主流的板材热轧设备为两辊、三辊、四辊、八辊热轧机,热轧机宽度在 1200 ~ 4060 mm;主流的板材冷轧设备为四辊、八辊可逆式冷轧机,冷轧机宽度在 1200 ~ 1780 mm。国内外主流的带材热轧设备为多机架热连轧机组,冷轧设备为二十辊 Sendzimir 冷轧机。达到成品尺寸的板材经热处理、板型处理和表面处理后则完成产品制备。
随着全球工业用钛需求量的增加,以及钛材在航空、航天、海洋、船舶领域的推广,钛板材类产品的产量与性能需求不断提升,促进了板材类新产品的开发和钛板、带、 箔材制备技术发展。首先,以高温钛合金为例,自 20 世纪 50 年代发展至今,钛合金板材产品的服役温度逐渐由 300 ℃提升到 650 ℃,使用部位也逐渐由飞机蒙皮表面升级到关键核心承力部件,如图 1 所示。1950 — 1960 年设计了 OT4 – 1(TC1)、OT4 (TC2)、Ti–6Al–4V(TC4)、BT6 等 在 200 ~ 400 ℃使用的钛合金,其薄板类产品大量应用于飞机薄壁钣金零件,Ti–6Al–4V 合金厚板和薄板也被应用于航空发动机宽弦空心风扇叶片制造。1960 —1970 年设计了 BT20(TA15)、Ti6242、Ti6246 (TC19)等在 400 ~ 500 ℃使用的钛合金,BT20(TA15)合金厚板产品通过机械加工应用于大型飞机结构件制备 ,而其薄板也广泛用于超塑成形带筋结构件。Ti6242 合金板材、锻件应用于航空发动机中低温压气机盘、叶片和叶轮,服役温度可达 500 ℃[27–28]。1970 —1990 年设计了 Ti6242S(TA19)、IMI834、Ti1100 等在 520 ~ 600 ℃使用的钛合金, IMI834 合金厚板、锻件应用于航空发动机中高温压气机机盘、叶片和叶轮,服役温度可达 550 ℃。Ti1100 合金板材用于航空发动机环形燃烧室筒体和高压压气机叶片和盘件,服役温度可达 600 ℃。1990 年至今国内设计了 Ti55(TA32)、Ti60 (TA33)、Ti65 等在 550~650 ℃使用的钛合金,Ti55(TA32)合金厚度板材、锻件用于国内航空发动机燃烧室筒体和巡航导弹弹体结构研制,服役温度可达 550 ℃。Ti60(TA33) 合金厚板用于航空发动机叶片、盘、 鼓筒等高温部件,服役温度可达 600 ℃。Ti65 合金薄板用于超音速飞机蜂窝结构和壁板,服役温度可达 650 ℃。此外,高强高韧钛合金板材类产品也被广泛应用于航空和海洋工程(图 1),Ti15333(TB5)合金薄板抗拉强度和延伸率可达 1375 MPa 和 5%,成形后应用于大型运输机管路和冷成形钣金零件。Ti5553 合金强度可达 1517 MPa, 用于飞机起落架。Ti62A 合金板材强度和断裂韧性可达 1134 MPa 和 72.79 MPa·m1/2,这种高强高韧损伤容限型钛合金板材应用于深海载人潜水器。最后,船用钛合金板材类产品的应用也呈现逐年增加趋势。以 TA5、Ti70(TA23)、Ti75(TA24)和 Ti80(TA31)为代表的船用钛合金在船体上应用的加工材类型主要为板材,包括桅杆、导流罩、耐压气瓶和壳体等结构部件,如 图 1 所示。整体而言,钛合金板材类产品应用十分广泛,除了以上列举的航空、航天、海洋、船舶领域,在兵器、装甲、化工、医疗器械、汽车等行业均应用广泛。钛合金板材制备技术则根据不同的使用需求,在外观、显微组织和性能上有不同的控制方法和技术要点。
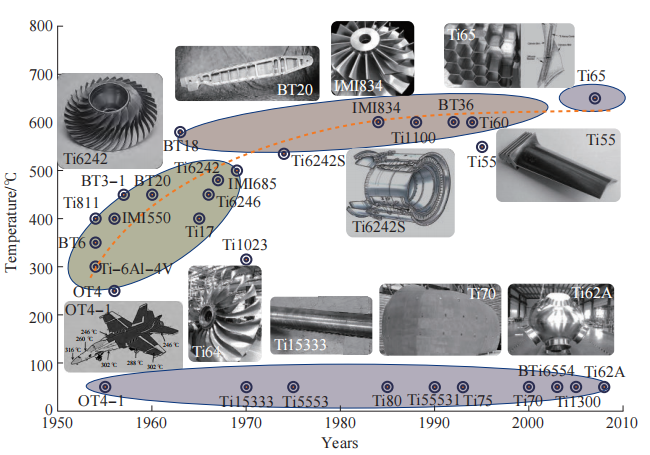
图 1 钛合金发展及其板材应用
1、钛合金板材制备技术概况
钛合金板材制备是一个通过冶金和物理方法得到满足目标需求几何外形和力学性能板材的过程。板材几何外形控制是基本的制备要求,包括厚度、宽度、长度、翘曲度、表面质量等。板材的力学性能取决于合金元素的添加和热机械过程(轧制、热处理),通过合金化和热机械过程调控组织形貌、 第二相类型、相比例和织构类型,以实现对力学性能的定量调控。
根据钛合金板材的厚度、β 相稳定系数 Kβ和热变形特性,其轧制工艺可以分为单相区热轧、两相区热轧、冷轧及三者的组合工艺,配合相应的热处理工艺可制备不同厚度和多种组织状态的板材(图 2)。在厚度控制上,厚板制备过程通常是在相变点附近轧制,通过 1 ~ 3 个火次直接热轧至成品厚度;薄板制备过程通常采用热轧至中间厚度,冷轧到成品厚度,再结晶退火后达到交货状态;难变形高合金化薄板通常采用包套叠轧(热轧)至成品厚度。在组织控制上,通过对轧制火次、轧制温度、变形量、热处理温度等工艺参数调整,可以实现对组织形貌的控制, 如图 2 所示。组织形貌决定了板材的力学性能,通常认为全片层组织具有良好的韧性、较高的蠕变强度和较低的裂纹扩展速率,双态组织 具有较高的疲劳寿命和良好的强塑性匹配,等轴组织具有较高的抗拉强度、良好的塑性和优异的超塑性。
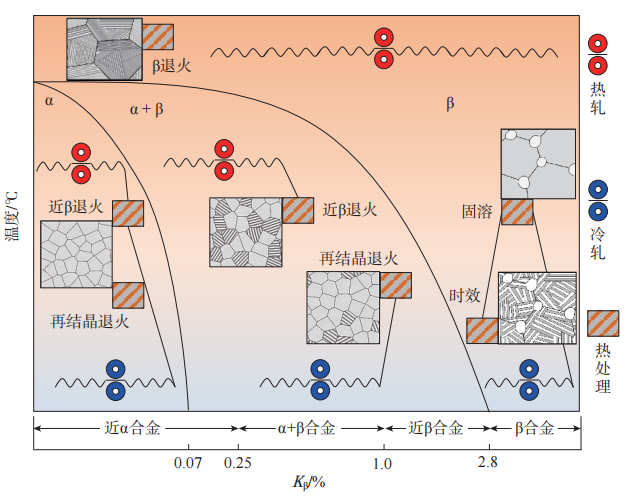
图 2 钛合金分类与板材制备工艺示意图
2、钛合金薄板制备技术现状及问题
受热轧机厚度控制精度和轧制力的限制,钛合金薄板的成品加工过程通常采用冷轧和包套叠轧制备技术。
2.1 冷轧钛合金薄板
由于常温下近 α 钛合金和 α + β 两相钛合金主要为 α 相,而 β 和近 β 钛合金主要为 β 相,相种类和相结构不同使不同钛合金的塑性加工能力和板材成形方式不同。图 3 为钛合金板材冷轧加工硬化曲线,可知不同类型钛合金的冷轧加工能力有较大差异,整体上随着合金化程度的提高,板材抗拉强度(Rm)越高,延伸率(A5)越低加工硬化过程越明显。纯钛和 β 合金的塑性成形能力有显著优势,冷轧变形量可达 80% 左右。受合金化的影响,TA5 近 α 合金和 TC6 两相合金冷成形能力较差,极限变形量分别为 26.5% 和 31.0%,超过极限变形量后板材表面和边部开始形成微裂纹。通过冷轧制备钛合金薄板主要分为两个步骤:第 1 步热轧至中间厚度;第 2 步冷轧加工板材至成品厚度。冷轧制备的钛合金板材,其表面质量、板材不平度、厚度精度等可以得到良好控制,因此冷轧制备技术在钛及钛合金薄板制备过程中得到广泛应用。
2.1.1 α 钛合金及 α + β 两相钛合金
图 4 为 α 钛合金和 α + β 两相钛合金通过冷轧制备技术加工薄板的工艺流程和组织演变情况。通常 α 钛合金和 α + β 两相钛合金冷轧薄板加工工艺如图 4(a)所示,此工艺在 TA10、TA18、TC1、TC2、TC4 等钛合金薄板制备过程中均有应用。钛合金锻坯经过单相区Ⅱ轧制,可以降低变形抗力,充分破碎锻坯的粗晶组织,并且提高轧制效率。Ⅲ均一化过程为加热至单相区然后快速冷却,主要是均匀化变形组织并且弱化形变织构,控制冷却速率可以实现对 α 片层尺寸的控制(冷却越快越细小) 和晶界 α 析出量的控制(冷却越快越不易析出)。Ⅳ两相区热轧至中间厚度(一般是热轧极限厚度),然后通过中间退火获得充分软化的再结晶等轴组织,为冷轧提供组织和性能条件。需要说明的是,随着热轧机组精度的提高,仅通过Ⅳ热轧过程也可制备出较薄板材。α 钛合 金、α + β 两相钛合金经过Ⅴ中间退火后,室温下主要为 α 相。Ⅵ冷轧变形过程主要是 α 相的变形过程,此过程主要通过控制板材的道次变形量和火次变形量,最终获得目标尺寸和性能的板材。不同钛合金板材的最优冷轧变形量是不同的,可通过绘制冷轧加工硬化曲线获得 (图 3),一般最优冷轧变形量为极限变形量(表面出现微裂纹时的变形量)的 60% ~ 80%,如 TC4 合金优化的冷轧火次变形量为 26.3%, TC6 合金优化的冷轧火次变形量为 25% ~ 27%。合理的冷轧变形量既有利于冷轧高效加工,又可在成品退火后得到均匀的再结晶组织。
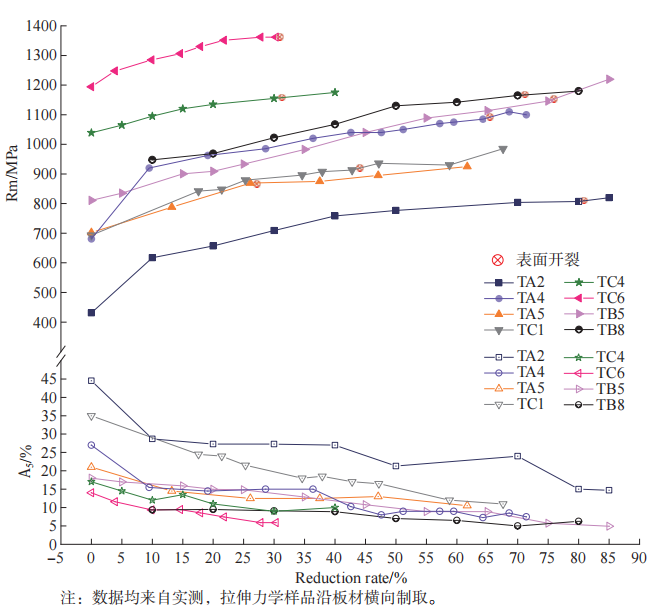
图 3 钛合金板材冷轧加工硬化曲线
α 钛合金和 α + β 两相钛合金在室温下主要由 α 相构成(体积分数 > 90%),因此这两类合金板材冷轧变形过程有相似的变形特征,如 TA1 与 TC4 板材,室温变形主要表现为 α 晶 粒的滑移变形和转动,晶粒拉长、破碎,形成冷轧变形组织。图 4(b)~ (d)为典型的全 α 相纯钛板材经中间退火后冷轧过程的组织演变、位相差演变和织构演变。随着轧制变形量由 10% 增加至 40%,显微组织沿轧制方向逐渐拉长,球状组织充分破碎,形成大角度晶界(图 4(b));小角度晶(LAGB)界由 8.4% 增加至 66.1%, 说明变形过程位错缠结塞积程度增加 (图 4(c));轧制过程板材形成双峰基面织构和基面织构(图 4(d))。
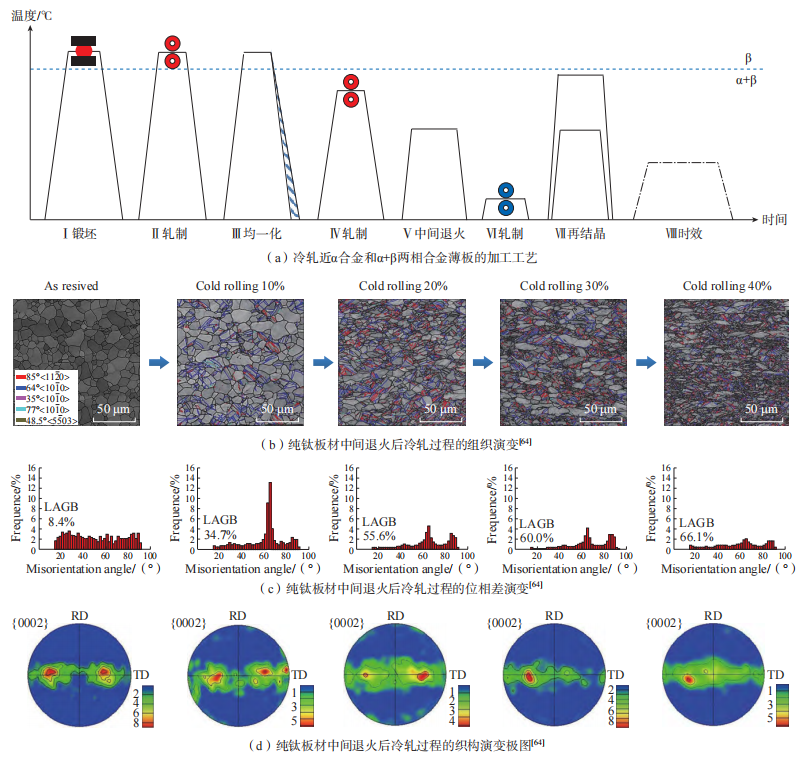
图 4 钛合金冷轧薄板的加工工艺和组织演变
对冷轧板材进行Ⅶ再结晶退火后显微组织演变主要包括再结晶过程和第二相的析出,形成再结晶织构和相变织构。以近 α 钛合金 Ti65 合金(相变点 1035 ℃)板材为例,通过对轧制状态 2.0 mm 板材控制热处理温度获得等轴和双态两种组织状态的板材(图 5)。对 Ti65 合金板材进行 800 ℃/30 min 和 990 ℃/30 min 热处理后,轧制变形态长条 α 组织迅速减少,得到细小的等轴组织(图 5(a)和(b)),随着温度升高,沿初生 α 相 αp 晶界处析出次生 α 相 αs 片层,αp 晶界清晰,晶粒尺寸增加(图 5(b))。经两相区高温(1020 ℃/30 min AC + 700 ℃/4 h AC )热处理后形成双态组织(图 5(c)),主要表现为 αp 含量不同,图 5(a)~(c)中 αp 体积分数分别为 90%、70% 和 30%, 随着热处理温度提高 αp 减少,αs 增加,最终形成双态组织。两相区热处理过程板材织构种类保持不变,包括 Ⅰ织构(1 - 21 - 0)织构,(1 - 21 - 0) 面 // 轧制面,// 轧向和Ⅲ织构 为(011 - 3)// 轧面的纤维织构。织构强度随着热处理温度逐渐演变, 高温固溶时效板材的织构强度明显增加。
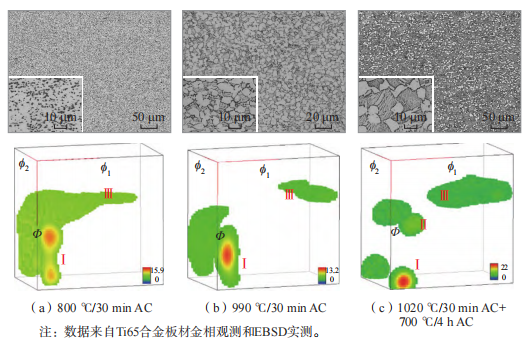
图 5 Ti65 合金板材不同热处理制度的显微组织与织构 3D–ODF 图
2.1.2 近 β 钛合金
图 6 所示为近 β 两相钛合金通过冷轧制备技术加工薄板的工艺流程和组织演变。通常 β 钛合金和近 β 钛合金冷轧薄板的加工工艺如图 6 (a)所示,此工艺在 TB5、TB6、TB8、 TB15 等钛合金薄板制备过程中均有应用。与 α 钛合金和 α + β 两相钛合金冷轧薄板的加工工艺(图 4 (a))的主要区别在于热轧过程无均一化处理和中间退火采用单相区固溶退火。近 β 钛合金相变点较低,两相区轧制温度较低,变形抗力较大,不利于板型和表面质量控制。因此,通常热轧过程Ⅱ选择单相区或相变点附近轧制,降低变形抗力,提高轧制效率。Ⅲ单相区固溶处理的主要原因在于避免低温热处理冷却过程时效强化,软化板材,为冷轧阶段提 供组织和性能基础。近 β 钛合金和 β 钛合金经过Ⅴ固溶退火后,室温下主要为 β 相(BCC 结构),室温下塑性良好,因此根据制备板材的厚度情况,通过Ⅲ固溶和Ⅳ冷轧工序多次反复循环,可实现较薄板材的制备 。
β 钛合金固溶处理后在室温下主要由 β 相构成(残余少量 α 相), 因此这类合金板材冷轧变形过程有相似的变形特征,如 TB5 合金和 Ti–23Nb–0.7Ta–2Zr 合金薄板, 主要表现为 β 晶粒的滑移变形,晶粒拉长、破碎,形成冷轧变形组织。典型的 β 钛合金(Ti–14.23%V–3.62%Al– 3.74%Sn–2.67%Cr–0.43%Si,质量分数) 不同冷轧变形量和再结晶退火后的显微组织,如图 6(b)和(c)所示,随着变形量的增加形成大量滑移带和应变局部化现象加剧,再结晶退火后获得均匀的等轴组织。近 β 钛合金 (Ti–3.5Al–5Mo–6V–3Cr–2Sn–0.5Fe, 质量分数)轧制和退火过程的织构演变,如图 6(e)~(h)所示,冷轧和退火过程形成 γ 纤维织构(<111> 晶向 // 轧面法向)。由于 β 钛合金优良的冷加工性能,可以实现超大冷轧变形和交叉轧制,如 TB8(β21S)亚稳 β 钛合金冷轧加工变形量可达到 80% 以上(图 3)。通常 β 钛合金和 近 β 钛合金冷轧变形量须达到 50% 以上才能充分变形获得均匀的轧制组织。
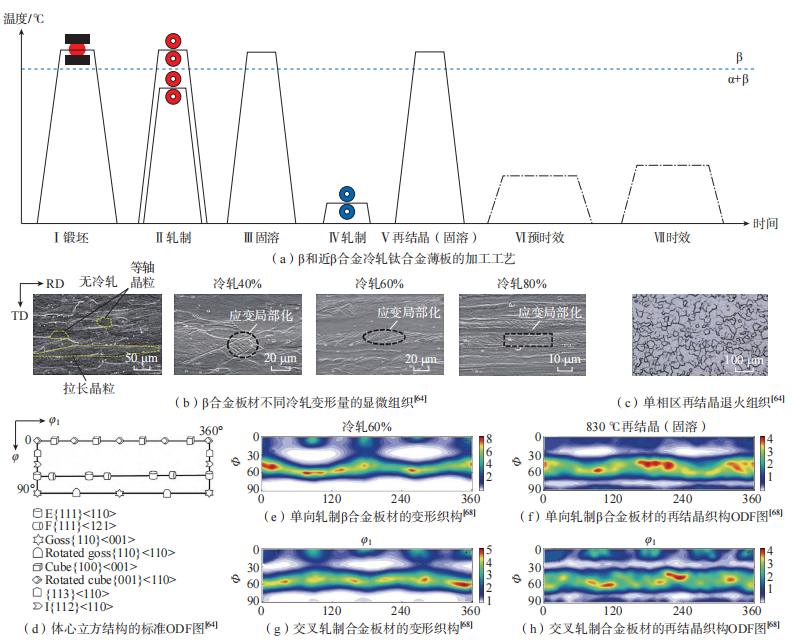
图 6 钛合金冷轧薄板的加工工艺和组织演变
2.1.3 冷轧制备技术现存问题
冷轧钛合金薄板受到轧制变形量、轧制方向的限制,通过冷轧制备技术加工的钛合金薄板易出现以下问题。
(1)加工效率低。以 TC4 为例,从 2.8 mm 冷轧至 1.0 mm,根据图 2 给出的 TC4 最优加工率(20% ~ 25%) 计算,需要 4 个轧程,中间需要进行 3 次退火和表面处理,效率低、资源浪费大。通过热轧叠轧技术、包套叠轧技术或卷带式生产可以提高加工效率。
(2)板材组织不均匀。HCP 结构 α 相具有 12 种滑移系,少于 BCC 结构 β 相的 48 种滑移系,而室温下 α 钛合金和 α + β 钛合金大部分为 α 相,HCP 结构限制了钛合金塑性变形能力和加工率。导致板材心部区域无法充分变形,出现组织不均匀现象。图 7(a)为 TC4 板材经 18.1% 冷轧变形后的显微组织,红框中区域不充分变形,最终导致退火后组织粗大且不均匀,影响板材的超塑成形过程。增大冷轧变形量和合理地提高热处理温度可以改善此类问题。
(3)板材翘曲度问题。现有产品对翘曲度的要求最高 <1.2%(TB5 合 金薄板),而通过冷轧制备技术加工的钛合金薄板,翘曲度可达 1.5% ~3%, 如图 7(b)所示。翘曲度不达标会导致自动焊接焊缝不对中、冷热成形不均匀。带张力轧制、液压弯辊、弯曲矫直和蠕变退火技术的应用可以有效改善薄板的板型问题,降低板材的翘曲度。
(4)板材易形成微区织构。由于热轧过程变形量和轧制温度的不良匹配,片层 α 取向球化过程形成取向近似一致的晶粒聚集区域,后续常规冷轧变形和退火过程无法彻底消除此类微观区域,此类大尺寸、多晶粒取向一致的区域称为微区织构 (Macro-zone,MZ)。图 7(c) 和(d)为 35% 冷轧变形后 750 ℃/30 min 退火的 1.0 mm 厚 TC1 合金板材的显微组织和再结晶分布图。从图 7(c)中可以看出 MZ 区呈现黑色条带状分布于显微组织中,MZ 区内部为小角度晶界聚集的未再结晶、 细晶区域。MZ 区内的细晶呈现出 相似取向,如图 7(d)所示。MZ 区在外力作用下易产生应力集中,会显著降低板材的疲劳性能。通过热轧半成品板材组织优化或增大冷轧累积变形量可以消除此类 MZ 区。
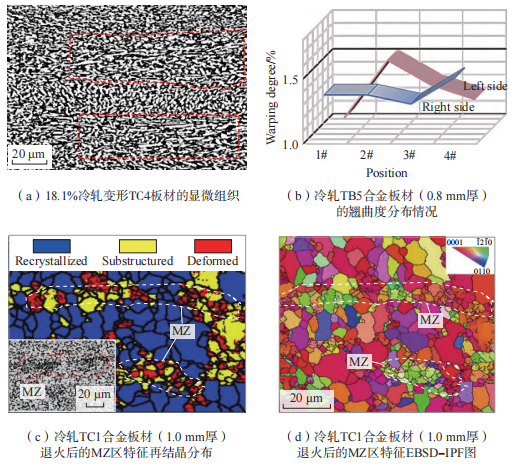
图 7 冷轧钛合金薄板的常见问题
2.2 包套叠轧钛合金薄板
2.2.1 制备工艺
包套叠轧制备钛合金薄板通常分两步进行。第 1 步是将板材换向轧制到中间厚度,大约是最终轧制厚度的 3 ~ 4 倍;第 2 步是将钛板以类似三明治的方式叠放装配在钢套中,加热轧制到所需的成品尺寸。换向轧制是为了使轧制板材的纵向和横向性能均匀。
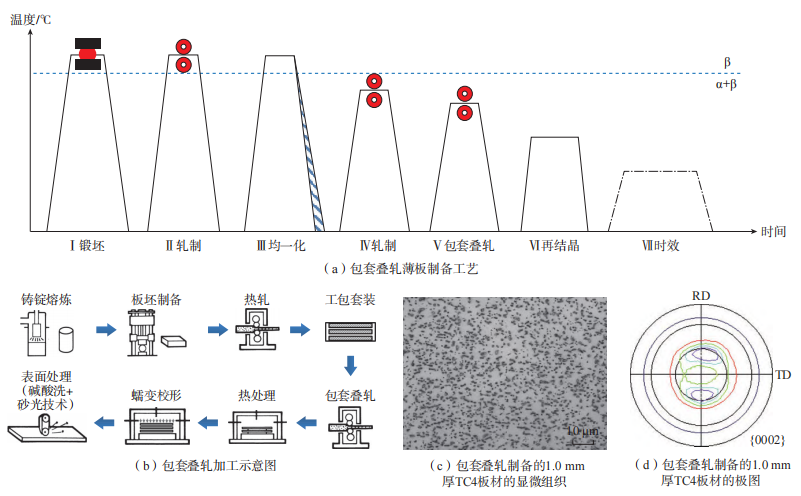
图 8 钛合金包套叠轧薄板的加工工艺和组织演变
图 8 所示为通过包套叠轧制备技术加工钛合金薄板的加工工艺和组织演变。钛合金薄板的包套叠轧制备工艺如图 8(a)所示,通常高合金化的近 α 钛合金和 α + β 两相钛合金薄板用此方法制备,如 TA15、TA32、Ti65 合金。包套叠轧前的加工工艺与冷轧薄板制备工艺相似,钛合金锻坯经过单相区轧制Ⅱ,单相区均一化处理Ⅲ后快速冷却,两相区热轧至中间厚度Ⅳ(一般是成品厚度的 3 ~ 4 倍),然后进行包套叠轧Ⅴ。主要是将多层叠放的钛板用钢套包套(图 8 (b)),进行整体加热和轧制。最后进行热处理和表面处理得到成品板材。包套叠轧技术的关键控制要点在于轧制温度、叠轧片数、板型和厚度均匀性。图 8(c)是用包套叠轧技术制备 1.0 mm 厚 TC4 板材的显微组织, 等轴组织均匀细小,平均晶粒尺寸为 3.9 μm,包套叠轧工艺的火次变形量远大于单片冷轧工艺,因此更容易获得细小均匀的显微组织。此外,包套叠轧工艺可以实现多次换向轧制,有利于获得对称性较好的基面织构,如图 8(d)所示,此类织构板材力学性能各向异性较小,有利于塑性成形和深加工应用。
2.2.2 包套叠轧制备技术现存问题
包套叠轧轧制技术的包套钢套可以实现保温轧制,对制备难变形钛合金、冷轧加工性差的钛合金板材,实用性很高。此外,包套叠轧轧制技术可以增加轧制厚度,实现热轧可控轧制薄板;提高轧制效率,热轧减小抗力,缩短薄板制备周期;实现多次换向轧制,控制板材织构;保温效果良好,可实现大变形,制备细晶板材。主要的工艺难点是多工序、流程复杂、过程控制难度大。
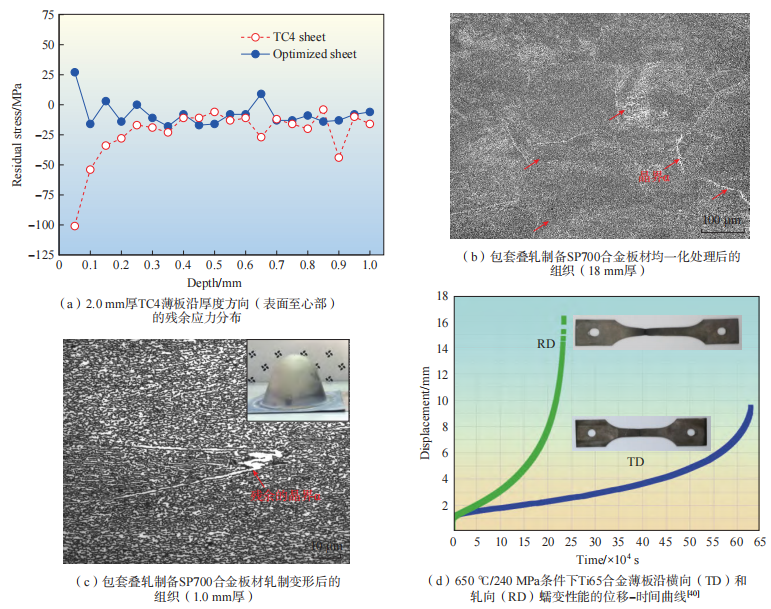
图 9 包套叠轧钛合金薄板的常见问题
通过包套叠轧制备技术加工钛合金薄板出现的主要问题包括 3 点, 如图 9 所示。
(1)板材残余应力较大。包套叠轧制备技术加工钛合金薄板火次变形量大,且轧制后板材表面处理工序复杂,轧制和表面处理(磨削、砂 光)过程均会引入残余应力,致使板材残余应力增大。如包套叠轧制备的 TC4 薄板(2.0 mm 厚度)沿厚度方向从板材表面至心部的残余应力分布,如图 9(a)红色曲线所示,板材残余应力较大,在 –101~ –4 MPa 之间。较大的板材残余应力不利于应用过程薄板的冷、热成形。通过再结晶热处理与真空蠕变处理结合的方法可以显著降低板材残余应力,处理后板材残余应力降低至–18~27 MPa,如图 9(a)蓝色实线所示。
(2)晶界 α 长条组织遗传。晶界长条 α 拉长、扭曲或断续的现象在 TC4、TA32、Ti65、SP700 等包套叠轧制备的钛合金薄板中均时有出现。主要是由于Ⅲ均一化过程(图 8(a)) 冷速控制不当,冷速过慢会导致晶界 α 沿原始 β 晶界大量析出并粗化,如图 9(b)所示,SP700 板材的均一化组织。长条晶界 α 组织一旦形成,在热轧过程很难彻底消除,即使累积变形量达到 90%,也只会扭着、弯曲或断裂,最终形成图 9(c)所示的异常组织,影响 SP700 材料的超塑成形性能。通过严格控制Ⅲ均一化过程的冷速避免晶界 α 相形成,或降低温度增大变形量轧制均可消除钛合金薄板的长条 α 异常组织。
(3)薄板力学性能各向异性问题突出。包套叠轧制备技术工艺设计时,由于轧制变形量和轧制方向设计不合理,易形成强横向织构或者双峰基面织构,导致沿板材不同方向的力学性能产生差异,影响板材的深加工和服役性能。这种各向异性问题在 TA32、TA15、TC4、Ti65 等合金薄板中常见,如图 9(d)为强横向织构的 Ti65 合金薄板沿 TD 和 RD 方向高温蠕变性能的位移 – 时间曲线,可以看出 TD 方向的高温蠕变持续时间约为 RD 方向的 3 倍。此外,强织构作用下 Ti65 合金板材沿 TD 和 RD 方向的蠕变变形机理不同,沿 TD 方向的蠕变变形受晶界滑移和扩散控制,沿 RD 方向的蠕变变形受位错滑移控制。通过控制轧制方向和优化换向轧制前后变形量比可以有效地改善板材各向异性问题。
3、结论
整体而言,钛及钛合金薄板的轧制制备技术在过去几十年间形成了较为完整的体系,通过冷轧和包套叠轧制备技术可实现钛合金国标牌号的大部分产品生产制备,国内基本实现了钛合金薄板自给自足、自主可控。但在高品质钛合金薄板制备技术上进展缓慢,高合金化板材加工效率低、高性能板材外观精度不良和各向异性较大、宇航级板材批次稳定性不良等问题依旧存在。另外,钛合金薄板自动化制备技术发展缓慢。轧制装备、控制方式发展缓慢,制备过程人工干预较多、自动化程度偏低,导致板材产品的生产效率低,人工成本高,板材组织性能的均匀性、批次稳定性不易控制。
关于钛合金板材制备技术的精细化控制和自动化研究工作从未停止。未来钛合金薄板制备过程的标 准化作业、控轧控冷技术应用、低成 本钛合金和高性能钛合金薄板制备技术开发将成为钛合金薄板加工行 业的重点工作。
相关链接