3D打印技术又被称为“快速成形技术”、“增
材制造技术”和“实体自由制造”等,其思想最早
在19世纪末出现于美国,并在20世纪80年代得
到应用与发展,至今已有30多年
[1-2]。3D打印技术
基于离散-堆积原理,采用与减材制造技术相反的
加工方式(逐层累加),通过操作计算机使材料逐层
累加,最终得到立体实物的过程
[3-7]。相比于传统的
减材制造技术,3D打印技术具有精度高、工艺简
单、自由度高、节约原材料、节省时间等优点,在航
空航天、工业、国防、医疗、汽车、电子等领域得到了广泛的应用
[8-9]。目前可用于3D打印的原料主
要有高分子材料(树脂、塑料、橡胶等)、金属材料
(铝合金、钛合金、不锈钢等)和非金属材料(陶瓷、石膏、
纸张等),其中高分子材料和非金属材料3D打印技
术起步较早、研究较多,技术相对成熟
[8]。而金属
材料3D打印技术则具备巨大的发展潜力,有专家
预测,在未来制造业中,金属材料3D打印技术将会
逐渐占据整个快速成形制造领域的主导地位[10]。

钛合金是一种重要的有色金属,具有密度小、
比强度高,以及良好的耐腐蚀性能、高温变形性能
和生物相容性等诸多优点,在航空航天、工业、国
防、医疗等领域得到广泛应用
[1,11-12]。传统的锻造
和铸造方法所制得的大型复杂的钛合金构件,由于
成本高、工艺复杂、材料利用率低以及后续加工困
难等不利影响,严重阻碍了其更为广泛的应用。而
3D打印技术采用与传统的减材制造相反的加工方
法,有着极高的材料利用率,相比传统的成形加工
方法有着极大的优势。目前对钛合金3D打印的研
究主要集中在材料、设备、技术以及工艺方面,但
是对零件的成形过程中缺陷问题的研究还处于初
步阶段。本文综述了国内外几种常用的钛合金3D打印技术,重点介绍了其在成形过程中缺陷的
分类、危害以及形成原因的研究现状,并结合国内
外的研究进展,对合金缺陷的改善方法进行探讨,
对钛合金3D打印的发展前景进行展望。
1、钛合金3D打印技术分类
当今,国内外常用的钛合金3D打印方法主要
有以下几种。根据热源不同可分为:以激光为热源
的激光选区烧结成形技术(selectivelasersintering,
SLS)、激光选区熔化成形技术(selectivelasermelting,
SLM)和激光近净成形技术(lasersolidforming,
LSF);以电子束为热源的电子束选区熔化成形技术
(electronbeamselectivemelting,EBSM)和电子束
熔丝沉积成形技术(electronbeamfusedeposition
forming,EBF3)。
SLS技术基于激光粉末床,运用激光有选择地
对粉末进行烧结,逐层叠加得到最终的实体零件。
具有材料利用率高、适用范围广、无需模具和支撑
结构、可直接制造任意形状复杂的结构件等优点;
但是由于烧结过程中粉末没有完全熔化,且之间没
有受到压力,因此孔隙无法消除,最终得到的制件
性能与传统制件相比仍有较大差距,存在残余应力
大、致密度低、强度低等缺陷
[10]。
LSF技术采用同步送粉方式,在激光作用下钛
合金粉末开始熔化、凝固,逐层堆积,可实现钛合金
零件直接制造。该技术具有低成本、周期短、无需
模具、材料利用率高等优点,但成形精度低,属
于“近净成形”,需经过后续加工才能得到最终的
制件
[9]。
在SLS技术基础上发展起来的SLM技术所使
用的激光功率更大,整个加工进程都处于保护氛围
的成形舱内,金属粉末完全熔化,成功弥补了
SLS技术只能成形低熔点金属、孔隙大、力学性能
差等缺点
[13-14];成形件的精度高和表面质量好,无
需后续加工,属于“净成形”,但是可成形的尺寸
有限,且成本较高。
EBSM技术与SLM技术的成形原理基本相似,
主要区别在于EBSM技术采用能量更大的电子束
为热源,整个成形过程均在真空环境中(≤10
–2Pa)
进行,能够很好地防止空气中其他有害杂质C、N、
O等的影响。具有成形速率快、能量密度高、无反
射、聚焦方便、真空无污染、尺寸精度高、力学性能
好等优点
[15-17]。
基于LSF技术基础发展起来的EBF
3技术,具
有成形效率快、无反射、材料和能量的利用率高、真
空无污染等优点,适合大中型钛合金零件的成形制
造修复。以丝材代替粉末为原料虽然避免了吹粉
问题,但是其成形精度差,需要后续表面处理
[18-19]。
表1为几种常见的钛合金3D打印技术比较。
综合对比,EBSM技术是未来最具发展前景的钛合
金3D打印技术,理由如下:(1)EBSM具有与
SLM技术相当的成形精度、表面质量以及良好的
力学性能,而且也克服了SLM技术不能成形大尺
寸零件的缺点;(2)整个成形过程均在真空环境下
进行,有效防止成形过程中C、N、O元素对材料的
污染;(3)采用功率更大的电子束代替激光束,不但
加快成形效率,而且降低生产成本。
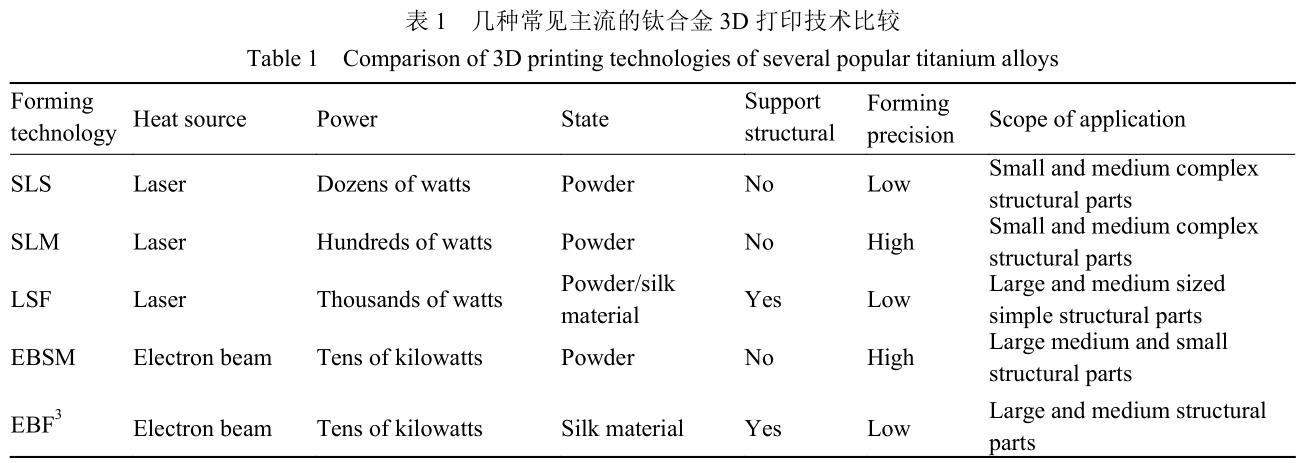
2、3D打印成形钛合金构件缺陷分析
采用3D打印技术制备钛合金,成功克服了使
用传统方法制备钛合金结构件时,所面临的费用
高、材料浪费严重、加工工艺复杂,以及后续加工
困难等不利因素,但采用3D打印技术成形钛合金
零件时,由于粉末/丝材特殊的加工性能,或者工艺
参数选择不当,工件容易出现球化、裂纹、孔隙以
及翘曲变形等缺陷。如图1所示,严重影响钛合金
的机械性能和成形精度,阻碍了钛合金3D打印技
术的发展。另外,缺陷无损检测是3D打印件能否
实现广泛应用的基础,也是影响3D打印技术进一
步发展的决定因素。

目前,国内外对3D打印件缺
陷进行无损检测的方法主要有
[20-22]:渗透检测、
X射线检测、磁粉检测和超声检测等。随着3D打
印件向结构大型化、复杂化和精细化方向发展,传
统的无损检测方法已经不再适用于3D打印件的缺
陷检测和分析,新型的无损检测技术工业CT检测
和激光超声在线无损检测相继问世。Plessis等
[23]
采用CT技术检测3D打印成形的复杂钛合金结构
件,成功检出了孔隙率仅为0.005%的微孔隙,这在
采用常规无损检测方法是几乎不可能检出的。国
内一专利
[24]发明了激光超声无损检测技术,利用激
光激励的超声表面波幅的变化检测3D打印过程中
产生的缺陷,实现制造过程同步对零件进行检测。
表2列出几种常见的无损检测技术比较。
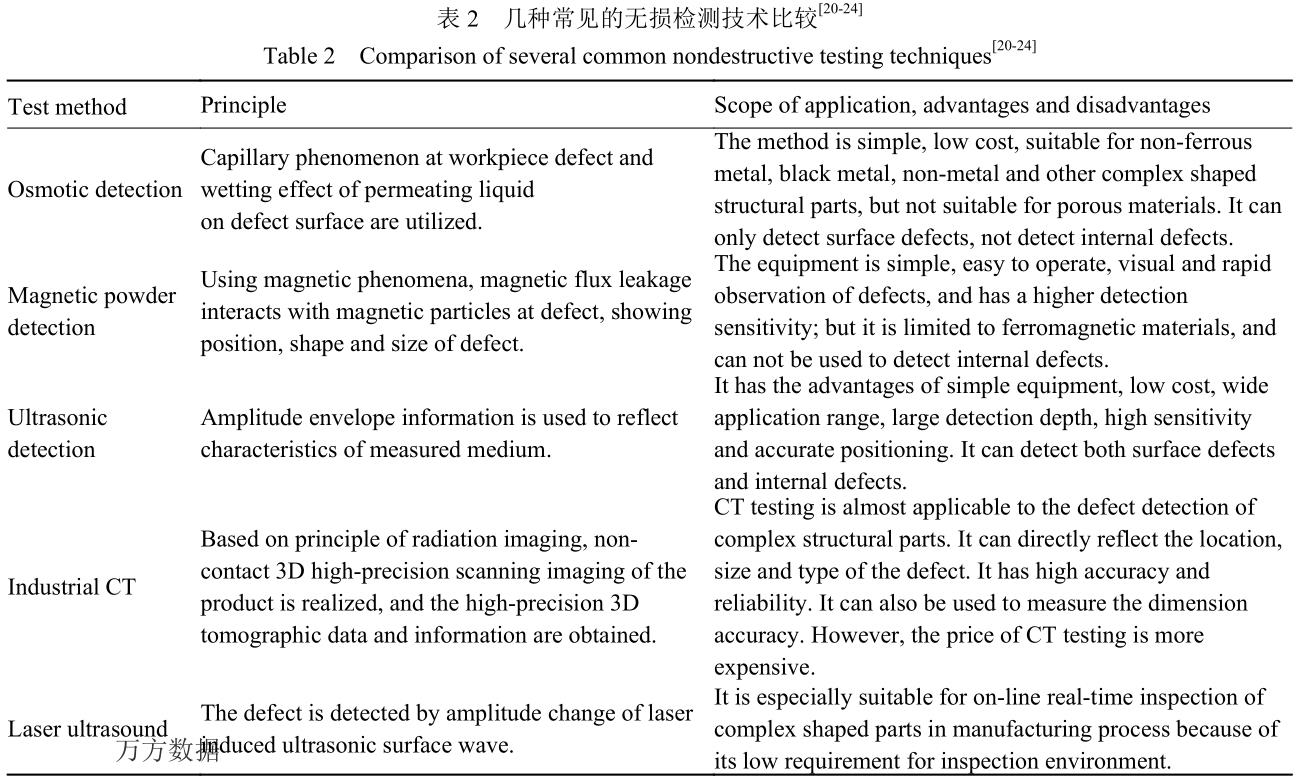
随着科学技术的进步,3D打印技术也在不停
地完善和发展,目前国内外逐渐对这些缺陷形成的
原因、分类及其危害进行了大量的研究,以期使钛
合金3D打印技术得到更为广泛的应用。
2.1球化现象
球化现象是3D打印金属材料成形过程中常见
的一种缺陷,是指金属粉末经激光或电子束熔化
后,不能均匀地铺展于前一层,而是产生大量相互
隔离的球状金属,这种现象被称为球化现象
[25]。该
缺陷主要的危害有以下两个方面:(1)导致金属件
组织内部存在孔隙,大大降低成形件的力学性能并
增加了表面粗糙度;(2)凝固后的金属球又会使下
一层的铺粉不均匀,且铺粉辊又会与前一层所产生
的金属球相互摩擦,不但会破坏成形件的表面质
量,而且当他们之间摩擦非常大时,铺粉辊将无法
动弹,致使成形过程终止。
近年来,越来越多的学者对球化现象形成原因
进行了大量的研究,但各持不同的意见。其中“液
态金属与固态表面的润湿问题”的说法较为普遍
接受
[26]。球化根据尺寸不同可分为大尺寸球化和
小尺寸球化,对大尺寸球化的形成原因归结于液-
固润湿问题。图2所示为液态金属与固态金属的
润湿示意图,当熔融金属液均匀铺展时,润湿角
θ<90°,固液金属润湿性良好,不会出现球化,当金
属液很难铺展于固态表面时,θ>90°,固液金属润
湿性差,产生球化反应。对于小尺寸球化的成因,
则认为是加工过程中发生液滴飞溅,在熔道或熔道
周围凝固成金属球,因为金属液飞溅相对较少,所
以金属球的尺寸也较小。Sallica等
[12]通过研究SLM
成形件Ti-6Al-4V的微观组织,发现过高的激光功
率会减小熔融金属的表面能,并导致球化现象的产
生。张晓博
[27]研究了加工环境对球化现象的影响,
认为成形气氛中的氧元素容易与熔融金属液发生
反应,形成一层致密的氧化物薄膜,该薄膜并不利
于金属液与固体基底润湿、粘合,容易导致球化的
产生,且球化现象随氧含量的增加,效果越明显;
他还研究了工艺参数对球化现象的影响,认为激光
功率过高,会出现“飞溅”,导致熔道间的金属球
大量出现,球化现象明显;扫描速率过快,激光在粉
末上停留的时间较短,金属液温度低,流动性及润
湿性差导致球化现象明显。沈以赴等
[15]认为球化
是由于液相表面张力大、黏度高,或熔融粉末与未
熔化的粉末颗粒和基板未发生浸润等的影响下产
生,进一步分析表明,激光快速成形过程中的氧气
是导致球化的直接原因。Gusarov等
[28]借助Plateau-
Rayleigh毛细不稳定理论
[29]指出:球化现象与熔池
的几何形状密切相关,在二维层面上,熔池长度与
宽度的比值大于2.1时,容易出现球化现象。
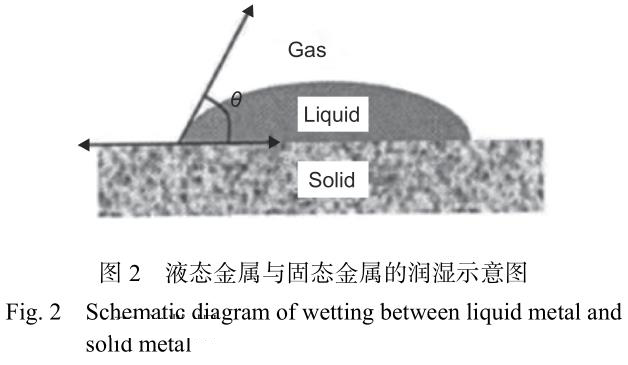
2.2孔隙
孔隙是成形过程中的另一种重要缺陷,对于一
些高性能致密的钛合金制件,由于孔隙的存在严重
降低了制件的力学性能和致密性,阻碍了钛合金的
广泛应用。对于孔隙的成因研究报道较多,上面谈
到的球化现象会引起制件的孔隙问题;裂纹也会导
致孔隙的形成,随着裂纹尺寸的不断变大,裂纹会
相遇连接,最后形成孔隙;另外粉末本身的缺陷也
会导致孔隙产生,在快速熔化和凝固过程中,空心
粉中含有的气体来不及逃逸,从而在成形件中残留
形成孔隙,此类孔隙形貌多为球形或类球形。
Gong等
[30]通过使用较大范围的工艺参数成形
Ti-6Al-4V合金,根据孔隙率大小将工艺参数进行
分类,并对孔隙的产生机理进行了讨论。薛雷等
[31]
分别采用未经干燥处理和经真空干燥处理的TC4
粉末对制件进行激光快速修复,认为修复过程中孔
隙的形成原因归因于以下两种:(1)粉末铺放时吸
附了空气中的其他杂质气体,在随后的成形过程中
受到激光/电子束加热、熔化后,又经快速凝固得到
成形件,其组织内部的气体析出不及时,保留在成
形件中并形成孔隙;(2)粉末不够干燥且存在水分,
在加热熔融后,一部分在熔池表面附近的水分以水
蒸气的形式蒸发逸出;远离熔池表面的另一部分水
分,与(1)类似的情况,由于气体来不及逸出,在制
件内部产生气孔。Zaeh等
[32]研究发现,使用高能量
密度的热源加工时,容易造成受热不均,当某部分
热量过高时,即使粉末还未引起球化现象,但仍会
形成孔洞,并且空洞在后续的加工过程中会变长。
Sallica等
[12]研究发现当激光功率过低时,导致熔化
不完全从而引起孔隙,影响致密性。
2.3裂纹
裂纹是激光快速成形过程中影响极大的一种
缺陷。在成形过程中,由于熔体过冷度大、冷却速
率快,在冷却过程中应力得不到释放而保留在制件
内,当应力集中超过材料屈服强度就会产生裂
纹
[27]。裂纹通常可分为微观裂纹和宏观裂纹两种,
其中成形件组织内部的微观裂纹一般是凝固裂纹,
归类为热裂纹;宏观裂纹则大部分表现为层间裂
纹,属于冷裂纹范畴。若制件中存在裂纹,将严重
影响制件的组织和力学性能。微裂纹尺寸相对较
小,会降低抗疲劳性能,缩短成形件的使用寿命;对
于粗裂纹而言,会影响零件的使用性能,甚至导致
零件直接报废。
周旭等
[33]研究了近α钛合金激光选区熔化成
形的开裂机理,得出如下结论:在残余应力作用下,
裂纹形成于侧壁缺口,在沉积层上沿着硬脆化合物
扩大。张升等
[34]采用交替扫描策略制备出TC4合
金试样,得出如下结论:SLM成形TC4合金过程中
裂纹主要为冷裂纹,具有典型的穿晶断裂特征,并
指出是由于SLM成形过程中激光熔化金属粉末受
热不均,致使成形件组织内部产生大的残余应力,
另外残余应力的作用下马氏体组织(抗裂强度低)
也会产生裂纹。Lukas等
[35]研究了工艺参数对SLM
技术的β型TNM-B1钛铝合金裂纹的成因,得出如
下结论:功率和扫描速率较低时,制件容易产生垂
直于熔池的裂纹,并认为在凝固过程中过快的冷却
速率所产生的残余应力是导致开裂的主要原因。
西北工业大学的张凤英等
[36]持相同的看法,也认为
是工艺参数选择不当,造成SLM制件内部粉末熔
合不良,导致制件发生开裂。刘延辉等
[37]研究了激
光3D打印TC4钛合金根部裂纹产生的原因,微观
组织如图3所示,认为TC4钛合金出现裂纹的根本
原因是根部存在组织缺陷、过大的残余应力、性能
分布不均以及预热温度不足等共同导致的。刘彦
涛等
[38]研究功能梯度材料TA15+Ti2AlNb合金激
光熔融沉积成形时发现,激光熔化沉积技术所制备
异种材料的界面为冶金结合,异种材料结合界面会
形成过渡区,过渡区通常是梯度复合结构的薄弱环
节,容易产生裂纹,此裂纹具有沿界面断裂的特征,
他们认为裂纹形成的原因是异种材料界面过渡区
通常会有对性能不利的第二相析出,导致材料易沿
界面断裂。
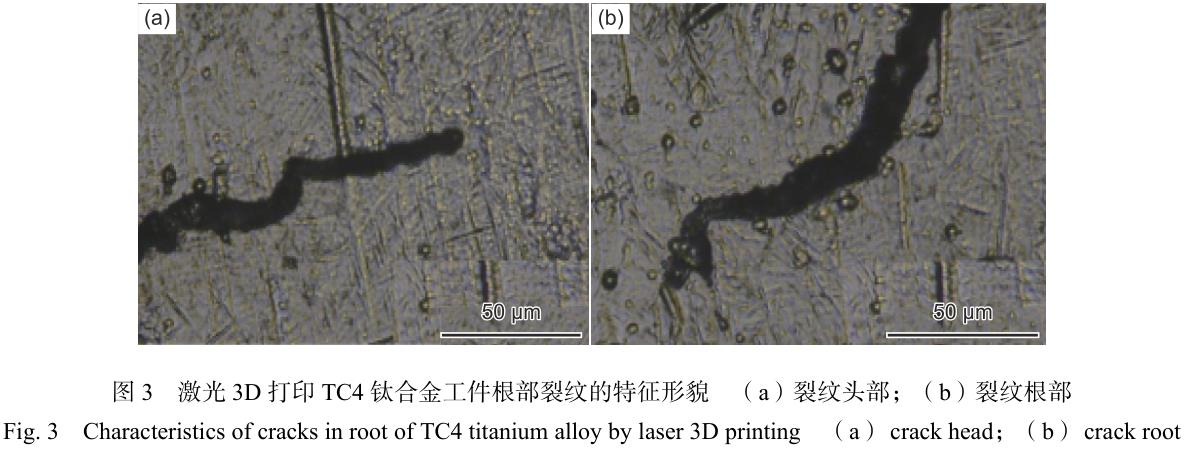
2.4翘曲变形
翘曲变形是基于粉末床3D打印成形技术的又
一个难题,经常出现在悬伸无支撑部分,其形成的
最根本原因是移动的激光点或电子束热源对粉末
床的不均匀加热,形成大的温度梯度,导致材料体
系收缩的不一致,主要是熔固收缩和温致收缩
[39,49]。
其中温致收缩是指成形件在打印完成后,冷却至常
温的过程中所产生的收缩,与材料本身的收缩率有
关,对产生翘曲变形作用较小;熔固收缩是由于粉
末经激光/电子束熔融后,经常产生的一种行为。主
要是因为成形过程中,粉末经加热后从熔融状态转
变为固态,温差变化较大,故熔固收缩相当严重
[39,43]。
翘曲变形对成形件的尺寸大小、成形精度、形位误
差等的影响很大,甚至会严重影响后续加工。
国内外针对钛合金翘曲变形的研究较少。吴
伟辉等
[40]对成形过程中造成翘曲变形的成因进行
了研究,翘曲变形示意图如图4所示,可以看出激
光作用的当前层(i)层,受到高温的作用处于塑性
状态,在凝固过程中过快的冷却速率,导致收缩变
形;第(i–1)层温度略低于第i层的温度,此时塑性
较差或处于弹性状态,在冷却过程中,其收缩变形
小于第(i)层的变形量,但是在第(i)层严重翘曲变
形的作用下,第(i–1)层也会发生大幅度的向上翘
曲变形。同理第(i–2)、(i–3)层也有相同的影响,只
是距离(i)层越远,对应层的收缩量越小,当距离(i)
层到达一定距离时,对应的层已不发生收缩变形,翘
曲变形终止。齐海波等
[41]采用电子束选区熔化成形
TC4钛合金成形件,认为扫描路径对成形件温度分
布的影响,导致热应力分布不均匀是翘曲变形产生
的主要原因。杨立宁等
[42]通过建立数值分析模型,
研究了在不同扫描路径和堆积速率下,所对应的热
应力场分布和变化行为,以及它们对制件翘曲变形
的影响。李守卫等
[43]分析了SLS技术成形过程中
的温度场与热应力场对翘曲变形的影响机理。
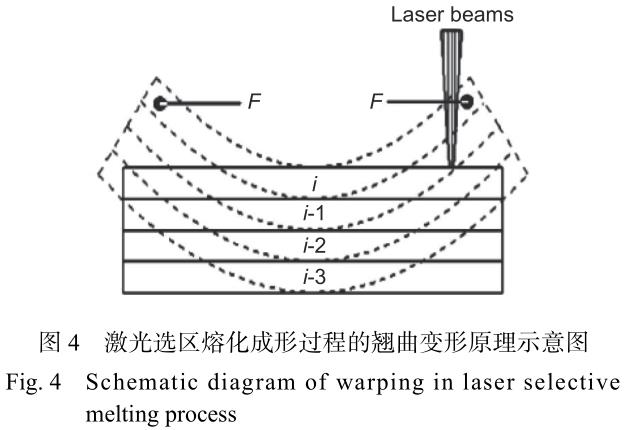
3、钛合金3D打印成形工艺优化
针对上述各种常见的合金缺陷,国内外学者运
用不同的原理,采用不同的工艺优化方法对合金缺
陷的抑制进行了探究。其中研究较多的方法主要
有:对粉末进行预热、优化工艺参数或者对制件进
行后续热处理等,都可以相应地改善合金的缺陷,
提高合金的组织性能。
3.1 3D打印工艺优化
使用不同的成形技术,加工不同的材料,其最
优的工艺参数各不相同,合理的设置工艺参数(激
光功率、扫描速率、扫描间距、扫描策略、层厚、预
热温度以及成形气氛等)能够明显减小球化、孔
隙、裂纹以及翘曲变形等缺陷。
Fischer等
[44]基于SLS技术使用高能量密度的
激光(Nd:YAG激光),对工业纯Ti进行了激光成
形。结果发现:制件的球化现象明显得到改善,且
成形件的孔隙率也得到提高。Cormier等
[45]认为采
用预热增加粉末黏度,将待熔化粉末加热到一定的
温度,可有效减少球化现象。张永志等
[46]研究发
现,通过对基板进行预热可降低熔池的凝固速率与
成形过程中的温度梯度,减小SLM成形合金中的
裂纹数量,但无法完全消除裂纹。梁晓康等
[47]采
用SLM成形技术制备TC4钛合金试样,研究了工
艺参数对残余应力的影响。结果发现:扫描策略对
表面残余应力分布有一定的影响,当线能量密度一
定时,随着填充间距的增加,成形层表面残余应力
有减小的趋势。周旭等
[33]研究了近α钛合金激光
选区熔化成形开裂机理及抑制研究,发现对工艺进
行优化,可减小组织内部的残余应力,从而可有效
抑制裂纹的产生;另外还研究了预热温度对裂纹抑
制的影响,发现裂纹的数量随着预热温度的提高逐
渐减少,在预热温度提高到350℃时,裂纹几乎完
全消失。陈静等
[48]研究了TC4钛合金的激光快速
成形,结果发现,氧含量严重影响成形件的工艺、表
面质量和开裂行为,当保证氧含量低于0.02%(质
量分数)时,得到的TC4薄板试样表面质量良好且
没有孔隙、裂纹等缺陷。傅蔡安等
[49]研究了扫描路
径对选择性激光烧结工艺成形件的翘曲变形的影
响,得出如下结论:优化了扫描路径不仅大大降低翘
曲变形量,而且大大缩短加工时间提高加工效率。
3.2后处理工艺优化
钛合金3D打印制件的后处理工序主要有退
火、热等静压、固溶时效、抛光、渗碳等,其中退火
的主要目的是减小零件内部的残余应力,热等静压
则可以减少组织内部的孔隙。汤慧萍等
[50]在粉末
床预热的基础上,结合随行热处理工艺
[51],也就是
在每完成一层粉末熔化扫描后,再经快速扫描实现
缓冷保温,从而通过塑性及蠕变使应力松弛,防止
应力应变累计,达到减小变形、抑制零件开裂、降
低残余应力水平的目的。张霜银等
[52]利用小孔释
放法对TC4钛合金(LENS技术成形)沉积态和热
处理后的残余应力进行研究,结果表明,经热处理
后,成形件的残余应力降低显著,且分布均匀。
Terner等
[53]认为金属粉末在制备过程中所存在的
氩气泡,在随后的成形过程中会导致孔隙的产生,
它一般呈细小球状,再经热等静压处理后,孔隙会
再次减小,但不影响材料的力学性能。
4、钛合金3D打印技术的发展趋势
钛合金3D打印技术作为一项前沿的制造技
术,集设计、制造于一体,近年来引起各界广泛关
注,并在航空航天、国防军事、生物医学、汽车高铁
等高精尖领域展示了广阔的应用前景,但是,相较
于传统制造技术起步较晚,发展历史仅30年左右,
与世界先进国家比较还存在很大的差距,比如:钛
合金零件的成形效率低、精度还未能达到高精水
平、设备和材料的制备成本高,以及仍未实现大规
模的工业、商业应用等问题,特别是成形件缺陷的
抑制问题。目前我国对零件的成形过程中存在的
缺陷问题,球化、裂纹、孔隙、翘曲变形等的研究还
处于初步阶段,仍有大量的研究工作急需进行。将
来钛合金3D打印技术的发展趋势如下:
(1)在材料方面,研制开发新型的球形钛合金
粉末的生产设备和制备工艺,提高钛合金粉末的质
量(粒度、球形度、流动性、夹杂气体等),进而改善
制件的组织和力学性能。此外,通过提高粉末的收
得率和粉末的回收再利用来降低成本。
(2)在设备方面,一方面应提高设备的成形效率、
成形精度,以及降低成本等;另外,还要研发大型的
工业级打印设备,逐步实现大规模生产和应用。
(3)在检测方面,伴随3D打印件向大型化、复
杂化和精密化方向发展,很多传统的无损检测方法
存在盲区,需要开发新型的无损检测技术;通过对
组织、缺陷实时监控的在线检测技术是未来重点的
研究方向之一;另外,建立和完善无损检测标准,
是3D打印技术广泛应用的依据。
(4)在工艺方面,进一步优化3D打印技术的
工艺,抑制成形过程中的缺陷,提高成形件的力学
性能。成形过程中零件内应力演变规律、变形开裂
行为以及缺陷产生机理等关键问题,仍然是未来需
要重点研究的问题。
参考文献:
[1]乔旭.钛合金增材制造技术的分析和未来趋势[J].中
国新技术新产品,2015(23):76.
(QIAOX.Analysisandfuturetrendoftitaniumalloy
augmentationmanufacturingtechnology[J].NewTech-
nologyandNewProductsinChina,2015(23):76.)
[2]伏欣.国内增材制造(3D打印)技术发展现状与研究
趋势[J].中国高新技术企业,2016(24):27-28.
(FUX.Thedevelopmentstatusandresearchtrendof
domesticaugmentedmaterialmanufacturing(3Dprint-
ing)technology[J].ChinaHi-techEnterprise,2016
(24):27-28.)
[3]谭语夷.3D打印的技术现状与发展趋势[J].中国机
械,2014(11):55.
(TANYY.Thetechnicalstatusanddevelopmenttrend
of3Dprinting[J].ChinaMachinery,2014(11):
55.)
[4]孙镇镇.3D打印材料及其发展问题与趋势[J].中国粉
体工业,2016(1):4-6.
(SUNZZ.3Dprintingmaterialsandtheirdevelopment
problemsandtrends[J].China’sPowderIndustry,
2016(1):4-6.)
[5]YEONGWY,CHUACK,LEONGKF,etal.Rap-
idprototypingintissueengineering:challengesandpo-
tential[J].TrendsinBiotechnology,2004,22(12):
643-652.
[6]曾亮华,刘继常.金属3D打印技术的发展分析[J].机械工程师,2016(3):42-44.
(ZENGLH,LIUJC.Developmentofmetal3Dprint-
ingtechnologyanalysis[J].MechanicalEngineer,
2016(3):42-44.)
[7]李涤尘,田小永,王永信.
增材制造技术的发展[J].
电加工与模具,2012(增刊1):20-22.
(LIDC,TIANXY,WANGYX.Developmentof
additivematerialsmanufacturingtechnology[J].Electric-
alMachiningandDie,2012(Suppl1):20-22.)
[8]祁斌.3D打印技术在船舶领域的应用[J].中国船检,
2016(6):94-100.
(QIB.Applicationof3Dprintingtechnologyinship
field[J].ChinaShipInspection,2016(6):94-100.)
[9]杨强,鲁中良,黄福享,等.
激光增材制造技术的研
究现状及发展趋势[J].
航空制造技术,2016,507
(12):26-31.
(YANGQ,LUZL,HUANGFX,etal.Research
statusanddevelopmenttrendoflaseraugmentationman-
ufacturingtechnology[J].AviationManufacturingTech-
nology,2016,507(12):26-31.)
[10]闫占功,林峰,齐海波,等.
直接金属快速成形制造
技术综述[J].机械工程学报,2005,41(11):1-7.
(YANZG,LINF,QIHB,etal.Summaryofdir-
ectmetalrapidprototypingmanufacturingtechnology[J].
JournalofMechanicalEngineering,2005,41(11):
1-7.)
[11]钱九红.航空航天用新型钛合金的研究发展及应用[J].
稀有金属,2000,24(3):218-223.
(QIANJH.Developmentandapplicationofnewtitani-
umalloysforaerospace[J].RareMetals,2000,
24(3):218-223.)
[12]SALLICALE,JARDINIAL,FOGAGNOLOJB.
MicrostructureandmechanicalbehaviorofporousTi-
6Al-4Vpartsobtainedbyselectivelasermelting[J].
JournaloftheMechanicalBehaviorofBiomedicalMater-
ials,2013,3(26):98-108.
[13]BIRSEREM,MOSKYITINGV,POLYAKOVA
N,etal.Industriallasercladding:currentstateandfu-
ture[J].WeldingImeraatonal,2011,25(3):234-
243.
[14]KRUTHJP,FROYENL,VAEMBERGHJV,etal.
Selectivelasermeltingofironbasedpowder[J].Journal
ofMaterialsProcessingTechnology,2004,149(1-
3):616-622.
[15] 胡孝昀,沈以赴,李子全,等.
金属粉末激光快速成
形的工艺及材料成形性[J].
材料科学与工艺,2008,
16(3):378-383.
(HUXY,SHENYF,LIZQ,etal.Processingand
materialformabilityofmetalpowderlaserrapidprototyp-
ing[J].
Material
Science
and
Technology,2008,
16(3):378-383.)
[16]陈济轮,杨洁,于海静.
国外高能束增材制造技术应
用现状与最新发展[J].航天制造技术,2014(4):1-
4+10.
(CHENJL,YANGJ,YUHJ.Theabroadapplica-
tionandlatestdevelopmentofhigh-energybeamadditive
manufacturingtechnology[J].SpaceManufacturing
Technology,2014(4):1-4+10.)
[17]刘海涛,赵万华,唐一平.
电子束熔融直接金属成形
工艺的研究[J].西安交通大学学报,2007,41(11):
1126.
(LIUHT,ZHAOWH,TANGYP.Studyondirect
metalformingbyelectronbeammelting[J].Journalof
Xi’anJiaotongUniversity,2007,41(11):1126.)
[18]陈哲源,锁红波,李晋炜.
电子束熔丝沉积快速制造
成形技术与组织特征[J].航天制造技术,2010(1):
40-43.
(CHENZY,SOUHB,LIJW.Rapidprototyping
andmicrostructurecharacteristicsofelectronbeamfuse
deposition[J].SpaceManufacturingTechnology,2010
(1):40-43.)
[19]黄秋实,李良琦,高彬彬.
国外金属零部件增材制造
技术发展概述[J].国防制造技术,2012(5):28-31.
(HUANGQS,LILQ,GAOBB.Overviewofthe
developmentofforeignmetalpartsmanufacturingtech-
nology[J].NationalDefenseManufacturingTechno-
logy,2012(5):28-31.)
[20]杨平华,高祥熙,梁菁,等.
金属增材制造技术发展
动向及无损检测研究进展[J].
材料工程,2017,45
(9):13-21.
(YANGPH,GAOXX,LIANGJ,etal.Develop-
menttrendofmetaladditivemanufacturingtechnology
andresearchprogressofnondestructivetesting[J].Ma-
terialsEngineering,2017,45(9):13-21.)
[21]赵静.机械零件缺陷的无损检测方法发展趋势[J].农
业装备与车辆工程,2005(9):39-40.
(ZHAOJ.Developmenttrendofnondestructivetesting
methodsfordefectsofmechanicalparts[J].Agricultural
EquipmentandVehicleEngineering,2005(9):39-
40.)
[22]肖永顺,王凤娟.
工业CT在3D打印领域的新应用
[C]//全国射线数字成像与CT新技术研讨会.
厦门:
[出版者不详],2014.
(XIAOYS,WANGFJ.Newapplicationsofindustri-
alCTin3Dprinting[C]//NationalSymposiumonRadio-
graphicDigitalImagingandCTNewTechnologies.Xia-men,China:[s.n],2014.)
[23]PLESSISAD,ROUXSGL,ELSJ,etal.Applica-
tionofmicroCTtothenon-destructivetestingofanaddit-
ivemanufacturedtitaniumcomponent[J].CaseStudiesin
NondestructiveTesting&Evaluation,2015,4(11):1-7.
[24]王晓,史亦韦,梁菁,等.激光超声在线无损检测增材制造零件的方法:CN106018288A[P].2016-06-17.
(WANGX,SHIYW,LIANGJ,etal.Methodsof on-linelaserultrasonicnondestructivetestingofaugmen-
tedmaterialsformanufacturingparts:CN106018288A
[P].2016-06-17.)
[25]GUD,SHENY.Ballingphenomenaindirectlasersin-
teringofstainlesssteelpowder:metallurgicalmechan-
ismsandcontrolmethods[J].Materials&Design,
2009,30(8):2903-2910.
[26]李瑞迪,魏青松,刘锦辉,等.
选择性激光熔化成形
关键基础问题的研究进展[J].
航空制造技术,2012,
401(5):26-31.
(LIRD,WEIQS,LIUJH,etal.Researchpro-
gressonkeybasicproblemsofselectivelasermelting
forming[J].
Aviation
Manufacturing
Technology,
2012,401(5):26-31.)
[27]张晓博.Ti合金选择性激光熔化成形关键技术的研究
[D].西安:陕西科技大学,2015.
(ZHANGXB.Researchonkeytechnologiesofselect-
ivelasermeltingofTialloy[D].Xi’an:ShaanxiUni-
versityofScienceandTechnology,2015.)
[28]GUSAROVAV,YADROITSEVI,BERTRANDP,
etal.Heattransfermodellingandstabilityanalysisofse-
lectivelasermelting[J].AppliedSurfaceScience,
2007,254(4):975-979.
[29]RAYLEIGHL.Ontheinstabilityofacylinderofviscous
liquidundercapillaryforce[J].TheLondon,Edinburgh,
andDublinPhilosophicalMagazineandJournalofSci-
ence,2010,34(207):177-180.
[30]GONGH,RAFIK,GUH,etal.Analysisofdefect
generationinTi-6Al-4Vpartsmadeusingpowderbedfu-
sionadditivemanufacturingprocesses[J].AdditiveMan-
ufacturing,2014(Suppl1/2/3/4):87-98.
[31]薛蕾,陈静,张凤英,等.飞机用钛合金零件的激光快
速修复[J].
稀有金属材料与工程,2006,35(11):
1817-1821.
(XUEL,CHENJ,ZHANGFY,etal.Rapidlaser
repairoftitaniumalloypartsforaircraft[J].RareMetal
MaterialsandEngineering,2006,35(11):1817-
1821.)
[32]ZAEHMF,KAHNERTM.Theeffectofscanning
strategiesonelectronbeamsintering[J].ProductionEn-
gineering,2009,3(3):217-224.
[33]周旭,周燕,魏青松,等.
激光选区熔化近α钛合金
开裂机理及抑制研究[J].
中国机械工程,2015,26
(20):2816-2820.
(ZHOUX,ZHOUY,WEIQS,etal.Studyon
crackingmechanismandinhibitionofnear-alphatitani-
umalloybyselectivelasermelting[J].ChinaMechanic-
alEngineering,2015,26(20):2816-2820.)
[34]张升,桂睿智,魏青松,等.
选择性激光熔化成形
TC4钛合金开裂行为及其机理研究[J].机械工程学报,
2013,49(23):21-27.
(ZHANGS,GUIRZ,WEIQS,etal.Studyon
crackingbehaviorandmechanismofselectivelasermelt-
ingformingofTC4titaniumalloy[J].JournalofMech-
anicalEngineering,2013,49(23):21-27.)
[35]
LUKASL,FRANKPS,UTAK,etal.Selectivelaser
meltingofabete-solidifyingTNM-B1titaniunaluminide
alloy[J].JournalofMaterialsProcessingTechnology,
2014(214):1852-1860.
[36]
张凤英,陈静,谭华,等.
钛合金激光快速成形过程
中缺陷形成机理研究[J].稀有金属材料与工程,2007,
36(2):211-215.
(ZHANGFY,CHENJ,TANH,etal.Studyonthe
defectformationmechanisminlaserrapidprototypingof
titaniumalloys[J].RareMetalMaterialsandEngineer-
ing,2007,36(2):211-215.)
[37]刘延辉,瞿伟成,朱小刚,等.激光3D打印TC4钛合金工件根部裂纹成因分析[J].理化检验:物理分册,2016,52(10):682-685.
(LIUYH,QUWC,ZHUXG,etal.Causeanalys-
isofcracksintherootofTC4titaniumalloyworkpiece
duringlaser3Dprinting[J].PhysicalandChemicalEx-
amination:Physical
Scroll,2016,52(10):682-
685.)
[38]刘彦涛,张永忠,陈以强,等.激光熔化沉积TA15+Ti2AlNb合金的组织与力学性能[J].
航空材料学报,2017,37(3):61-67.
(LIUYT,ZHANGYZ,CHENYQ,etal.Micro-
structureandmechanicalpropertiesoflasermeltingde-
positedTA15+Ti2AlNballoys[J].JournalofAeronautic-
alMaterials,2017,37(3):61-67.)
[39]帅昌俊.选择性激光烧结翘曲变形抑制研究[D].武汉:华中科技大学,2007.
(SHUAICJ.Studyoninhibitionofwarpageofselect-
ivelasersintering[D].Wuhan:HuazhongUniversityof
ScienceandTechnology,2007.)
[40]
吴伟辉,杨永强,毛星,等.激光选区熔化增材制造金
属零件精度优化工艺分析[J].铸造技术,2016(12):
2636-2640.
(WUWH,YANGYQ,MAOX,etal.Processop-
timizationforprecisionmanufacturingofmetalpartsby
laserselectivemeltingandaddition[J].CastingTechno-
logy,2016(12):2636-2640.)
[41]
齐海波,杨明辉,齐芳娟.扫描路径对电子束选区熔化
TC4成形件性能影响的数值模拟[J].焊接学报,2009, 30(8):5-8.
(QIHB,YANGMH,QIFJ.Numericalsimulation
oftheeffectofscanningpathonthepropertiesofelectric-
allymeltedTC4parts[J].ActaWelding,2009,
30(8):5-8.)
[42]杨立宁,单忠德,戎文娟,等.金属件熔融堆积3D打
印过程热应力场数值模拟[J].铸造技术,2016(4):
753-758.
(YANGLN,SHANZD,RONGWJ,etal.Numer-
icalsimulationofthermalstressfieldin3Dprintingpro-
cessofmetalmeltdeposition[J].FoundryTechnology,
2016(4):753-758.)
[43]
李守卫,沈以赴,顾冬冬,等.
选择性激光烧结金属
件翘曲与开裂问题的研究进展[J].
激光杂志,2005,
26(5):4-6.
(LISW,SHENYF,GUDD,etal.Progressinre-
searchonwarpageandcrackingofmetalpartsinselect-
ivelasersintering[J].LaserJournal,2005,26(5):
4-6.)
[44]
FISHCHERP,ROMANOV,WEBERHP,etal.Sin-
teringofcommerciallypuretitaniumpowderwithaNd:
YAGlasersource[J].ActaMaterialia,2003,51
(6):1651-1662.
[45]
CORMIERD,HARRYSSONO,WESTH.Character-
izationofH13steelproducedviaelectronbeam
melting[J].
Rapid
Prototyping
Journal,2004,10
(1):35-41.
[46]
张永志,侯慧鹏,彭霜,等.激光选区熔化Hastelloy
X合金的显微组织与拉伸性能的各向异性[J].航空材
料学报,2018,38(6):50-56.
(ZHANGYZ,HOUHP,PENGS,etal.Aniso-
tropyofmicrostructureandmechanicalpropertiesof
HastelloyXalloyproducedbyselectivelasermelting[J].
JournalofAeronauticalMaterials,2018,38(6):50-
56.)
[47]
梁晓康,陈济轮,严振宇,等.激光选区熔化成形TC4
钛合金表面粘粉及残余应力研究[J].
电加工与模具,
2016(5):52-55.
(LIANGXK,CHENJL,YANZY,etal.Studyon
surfaceadhesivepowderandresidualstressofTC4titani-
umalloyformedbylaserselectivemelting[J].Elec-
tromachiningandMold,2016(5):52-55.)
[48]
陈静,杨海欧,汤慧萍,等.成形气氛中氧含量对TC4
钛合金激光快速成形工艺的影响[J].
中国材料进展,
2004,23(3):23-26.
(CHENJ,YANGHO,TANGHP,etal.Effectof
oxygencontentinformingatmosphereonlaserrapidpro-
totypingprocessofTC4titaniumalloy[J].Progressof
MaterialsinChina,2004,23(3):23-26.)
[49]
傅蔡安,陈佩胡.
选择性激光烧结的翘曲变形与扫描
方式的研究[J].铸造,2008,57(12):1237-1240.
(FUCA,CHENPH.Studyonwarpagedeformation
andscanningmodeofselectivelasersintering[J].Cast-
ing,2008,57(12):1237-1240.)
[50]汤慧萍,王建,逯圣路,等.
电子束选区熔化成形技
术研究进展[J].中国材料进展,2015,34(3):225-
235.
(TANGHP,WANGJ,LUSL,etal.Researchpro-
gressofelectronbeamselectivemeltingtechnology[J].
ProgressinMaterialsinChina,2015,34(3):225-
235.)
[51]
TANGHP,YANGGY,JIAWP,etal.Additive
manufacturingofahighniobium-containingtitaniumalu-
minidealloybyselectiveelectronbeammelting[J].Ma-
terialsScience&Engineering:A,2015,636:103-
107.
[52]张霜银,林鑫,陈静,等.热处理对激光立体成形TC4
残余应力的影响[J].稀有金属材料与工程,2009,38
(5):774-778.
(ZHANGSY,LINX,CHENJ,etal.Effectofheat
treatmentonresidualstressoflaserstereoforming
TC4[J].RareMetalMaterialsandEngineering,2009,
38(5):774-778.)
[53]
TERNERM,BIAMINOS,EPICOCOP,etal.Elec-
tronbeammeltingofhighniobiumcontainingTiAlal-
loy:feasibilityinvestigation[J].SteelResearchInterna-
tional,2012,83(10):943-949.
相关链接